掌握程序
制订:
日期:
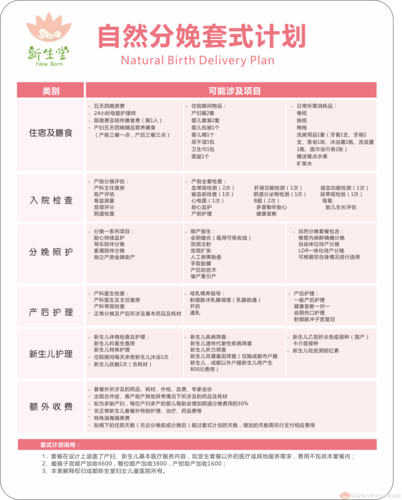
审核:
日期:
批准:
日期:
受控印章:
1.目的:
为达成公司目标,知足客户订单交期之需求,合理有效的安排生产, 并有效的对物料进行管控,特制订本程序。
2.适用范围
适用于本公司所有订单的生产操持和物料掌握。
3.权责
3.1.市场部:卖力订单评审、接单及发卖操持的制订。
3.2.PMC:卖力制订物料操持,跟催物料定期入库;编排生产操持,跟进产成品定期入库。
3.2.1.PC(操持员):卖力生产操持的拟定及进度掌握。
3.2.2.MC(物控员):卖力制订物料需求操持和跟进物料到位的进度。
3.3.生产部:卖力生产操持的实行及生产作业的掌握。
3.4.采购部:卖力物料的采购、跟催。
3.5.工程部:卖力产品标准、作业规范等工程资料作业。
3.6.仓库:卖力物料的收料、备料、发料等作业。
3.7.品质部:进料、制程、出货的考验及品质非常的剖断。
4.定义:无
5.内容
5.1.订单吸收和评审
5.1.1.业务部依《订单评审掌握程序》, 将已核准的客户订单或发卖操持单分发至PMC。
5.1.2.PMC订单审核和评估:
5.1.2.1.PMC对业务每天下达的《进货核对单》的精确性进行审核,MC确认物料哀求,PC确认生产哀求,如单据禁绝确或不合理则与业务协商进行修正。
5.1.2.2.物料期确认:确认物料在数量和交期方面是否能知足,如不能知足则组织采购确认最快交期。
出货期确认: PMC职员依据业务订单出货日期、物料交期及工程部制订的产品标准工时,评估产能负荷,确认成品交期等是否能知足。如不能知足则需组织产能评估!
5.1.3. 产能评估:以业务的预测或实际吸收的未完成订单为生产目标,由PMC主导,组织采购、生产、工程、业务等各干系部门对产能负荷进行评估,以决定是否进行外发或长期操持即增加人力和设备。
5.1.3.1.产能负荷评估结果为本公司生产能力或机器设备不能知足客户哀求时,PMC应下外发加工申请单,审批后由采购部联系外发加工单位进行外发加工,详细操作依《外发加工掌握程序》进行。
5.1.4.PMC在订单评审完成后复印分发给各干系部门。
5.2.生产操持拟定、分发
5.2.1.月产出操持的体例:每月5日前由PMC根据以往生产古迹和业务预测拟制,综合考虑公司产能负荷、原材料、工模具及设备状况,体例完成《月产出操持》要经部门卖力人、业务副总核准后才能分发至各干系部门。
5.2.2.日生产操持的编排:PMC以“月产出操持”为目标,根据订单哀求交付期的先后顺序及轻重缓急,在预定生产期前确认生产条件“人、机、料、法、环”是否完备,即核查工模具状况、设备状况、生产线负荷状况、原材料进厂状况等,同时整合兼顾各机型的工艺哀求,体例各工序“日生产排程”。《日排程操持》需备注投入期和哀求产出期、生产任务制令单号。
5.2.3.生产操持的变更或插单。
5.2.3.1. 《月产出操持》或《日排程操持》分发后,如遇以下环境PMC应予以调度:
A.客户增加、减少或取消订单生产量时;
B.由于客户紧急需求而产生的急单,可于订单评审阶段,由市场部、PMC、生产等部门相互折衷,进行生产操持的调度或换单;或由PMC、采购、仓库等部门先行备料,作插单准备。
C.原材料供应无法合营时;
D.制程及其它成分变动导致操持无法履行时;
生产部门因物料缘故原由或其它生产条件导致“日排程操持”无法实行时,应立即以《生产非常联结单》与PMC进行沟通,由PMC根据实际状况进行生产操持的调度。
E.其它不可预知事变导致操持需变动时。
5.2.3.2.生产操持变动时,PMC应对原来已发出的《月产出操持》或《日排程操持》撤消作废,对原操持及变动后的差异考量后,重新分发新的《月产出操持》或《日排程操持》
5.3.生产操持的实行。
5.3.3.《日排程操持》打印后至少提前一个事情日下达给生产主管和仓库主管签核,日操持对应的生产投料单在打印后下同时发给仓库签收。
5.3.4.仓库签收和核对《生产投料单》后,按生产哀求的日期及所须要物料,及时进行备料动作。
5.3.5.各生产主管签核“日排程操持”后,即按《日排程操持》的生产顺序对生产条件再确认,同时物料员依《日排程操持》对应的生产任务制令单号到仓库及时领料后安排生产。
5.4.生产操持进度掌握。
5.4.1.外发加工半成品,PMC应督匆匆采购跟催外发加工厂商按承诺期送货,确保在本公司生产上线前将委外产品交验入库,以便低廉甜头生产作业的顺利进行。
5.4.2.生产部门随时申报请示生产进度给PMC,同时PMC随时上各产线不雅观测生产进度。
5.4.3.生产部门逐日填写当日各制程、生产线的“生产日报表”,并且需及时上报给PMC以便对生产进度进行汇总追踪。
5.4.4.对任何不能达成操持生产进度的非常情形,PMC应哀求生产部门立即处理,并只管即便达成哀求进度。如相同非常在一个生产周期(常日为一个月)发生两次以上,PMC应哀求生产部门反省改进,详细参考《纠正和预防方法》履行。
5.5.生产操持完成。
5.5.1. 成品入库:生产部门将完成品包装完后填写《成品入库单》送QA考验,OK后,物料员将完成品送打包组进行入库交卸,完成生产。
5.6.物料操持制订。
5.6.1.物料干系根本资料的吸收。
研发需在业务下单前供应各产品的正式BOM给PMC,同时按确定好的生产工艺将BOM掩护进K3,采购需供应各物料的采购属性,如紧急采购周期、正常采购周期、最小采购批量、最小包装量、外发电子料损耗率,并安排将物料属性掩护进K3。
5.6.2.外购摄像机及干系物料操持
5.6.2.1.外购摄像机或部分非常用配件依照《进货核对单》按单及时制订外购物料操持。
5.6.2.2.常用配件。
常用配件如PC01等依照历史接单记录、公司的发卖策略、产品的生命周期,按单个采购周期备安全库存,两个采购周期备最低库存,两个月的用量为最高库存,综合实际接单情形和物料采购属性,制订物料操持。
5.6.2.3.包材物料。
包材物料为通用物料,依照历史接单记录、公司的发卖策略、产品的生命周期,按单个采购周期备安全库存,两个采购周期备最低库存,两个月的用量为最高库存,综合实际接单情形和物料采购属性,制订物料操持。
5.6.2.4.客制物料。
客制物料由MC反馈给业务实际需求,业务与客户确认采购操持,经副总审批后,MC按照审批后的采购申请作为终极物料操持。
5.6.3.低廉甜头产品物料操持
5.6.3.1.备用库存操持申请
5.6.3.1.1.《套料安全库存操持标准》申请:MC依据历史接单记录、公司的发卖策略、产品的生命周期申请备用一定周期(可定为10天)的套料安全库存标准,上报部门主管和副总审批。
5.6.3.1.2.《套料最底库存操持标准》申请:MC依据历史接单记录、公司的发卖策略、产品的生命周期,针对长交期物料(外购PCBA、委外PCBA、遥控器、五金塑胶外机构件等),申请备用《套料安全库存操持》外加单个采购周期(可定为30天)的套料最底库存标准,上报部门主管和副总审批。
5.6.3.1.3.《套料备料操持》的申请:MC依据历史接单记录、各低廉甜头产品中物料最长的采购周期、公司的发卖策略、产品的生命周期,综合《套料安全库存操持》和业务实际未完成订单数量,针对长交期物料(外购PCBA、委外PCBA、遥控器、五金塑胶外机构件等),在每个月尾或月初,申请备用两个采购周期(单个采购周期目前为一个月旁边)花费的《套料备料操持》,上报部门主管和副总审批。
5.6.3.2.备用库存物料操持
5.6.3.2.1.套料备料物料操持
PMC依据《套料备料操持》和BOM,结合物料采购周期、MOQ、MPQ等制订长周期物料申请操持。
5.6.3.2.2.其他短采购周期的物料操持(如:配线、构造配件、包材等),MC根据《套料安全库存操持标准》和BOM,同时依据单个物料的两个采购周期,结合物料采购周期、MOQ、MPQ等制订短周期物料申请操持。
5.6.4.MC接管业务月初的FCST或平时的正式发卖订单, 结合《套料备料操持》库存结存情形和《套料最底库存操持标准》,同时依据产品BOM,剖析长周期套料及短周期物料是否短缺, 制订物料申请操持。
5.6.5.物料操持调度
物料操持在以下情形下需进行调度:
A.公司策略调度
B.业务FORECAST骤减或者骤加
C.发卖订单骤减或者骤加
D.发卖订单取消或增加
E.其它不可预知事变导致操持需变动时
物料操持调度均哀求在K3中进行采购订单和采购申请单确认和处理。
5.7.物料的请购。
5.7.1.PMC依据物料需求操持在K3系统里提交《物料申请单》或《委外申请单》,哀求对每一张请购单进行简明扼要的来源和利用情形描述,如是大宗物料需备注“分批送货”、“待关照送货”等字样,由PMC主管进行初步的审核后(须要对每一张请购单里面所请购物料的种别,数量进行仔细的核对、确认。),再转副总做末了审批。
5.8. 物料操持的实行。
5.8.1.MC需跟进采购部及时(哀求在一个事情日内)下达“采购订单”,采购部依《采购掌握程序》处理采购订单。
5.8.2.哀求采购在两个事情日内依请购单哀求的数量、日期确认交期。
对付外购摄像机和配件,采购部在FLASHFXP回答《进货明细表》,并按照回答的交期跟催良品入库存;对付小件物料和委外PCBA,PMC将《物料操持表》共享在FLASHFXP给采购进行回答;对付大宗物料(请购单备注“分批送货”、“待关照送货”的),PMC在每周三前订定《周送货操持》共享在FLASHFXP给到采购回答。
5.8.3. MC必须每事情日定期(每事情日放工前)和不定期(接单后及时)确认现有接单是否够料,考虑实际物料短缺数并同时安全库存或最低库存,如采购回答的交期未能知足实际的生产操持需求韶光,PMC须要求采购重新确认交期并更新回答。
5.8.4.MC必须督匆匆采购按照最新的交期跟催良品物料送货,需督匆匆采购确认每天估量的到料信息(送料明细),并将信息传达到仓库原材料收料员和IQC。
5.9.物料操持的进度掌握
5.9.1.物料到厂后由仓库职员依《物料吸收程序》进行收料作业, IQC按《来料考验掌握程序》进行考验。
5.9.2.MC督匆匆采购跟进一样平常的物料,哀求仓库及时收货并在两个小时内对完货,哀求IQC当天之内必须考验完成,最迟二个事情日内必须完成考验;对付特急物料,哀求2个小时内完成考验;对付紧急物料,哀求4个小时内完成;若为生产急需物料(简称"急料"),物控要开内部联结单到仓库和IQC, 加快进料上线的进度。
5.9.3.对付当来料涌现非常时,MC需在吸收到品质开具给采购的《来料非常报告》后,及时进行确认是否可退,当急料涌现非常时,MC需主动找采购、品质、工程、生产或业务等干系部门确认是否可特采或加工知足紧急订单或知足生产利用。
5.9.4.物料在品质剖断OK后,由仓库办理入库。物料若NG时,采购需于一个事情日内与供应商确认交期并回答。MC依来料末了的良品交期作为打算交期达成率的来料交期。
5.9.5.必要时MC统计采购的交期达成率,对任何不能达成操持进度的非常情形,PMC应哀求采购部门立即处理,并只管即便达成哀求进度。如相同非常在一个生产周期(常日为一个月)发生两次以上,PMC应哀求采购部门反省改进,详细参考《纠正和预防方法》履行。
5.10.物料统筹管控
5.10.1.MC剖析订单欠料状况,回答齐套报告给PC作为生产排程的物料依据,再次确认日排程操持干系的投料单物料的齐套性,打印并发放投料单给仓库备料,同时跟进仓库的发料进度和折衷发料过程中的物料非常。
5.10.2.当生产部在生产时,若来料不良过高时, 生产部知会IQC关照厂商换料; 若为制程损耗过大时, 生产部该当开《非常联结单》到MC,并开具《超领物料申请单》申请追加备料。
5.10.2.1.《超领物料申请单》须要经部门主管审核,物控确认,厂长核准后,交仓库发料。
5.10.2.2.如损耗超过所备的损耗量时物控需及时追加物料的请购, 以知足订单的生产。
5.10.3.物控除正常知足从接单到出货全体物料状况的掌控和跟催外,还须要预防呆滞料的产生和对库存的呆滞料进行缘故原由剖析,其处理作业流程请参考 《库存呆滞料处理作业准则》。
5.10.4.对任何生产过程中产生的表单,按《记录掌握程序》予以保存。
6.干系文件
6.4.《订单评审掌握程序》 QH-QP-07
6.5.《生产过程掌握程序》 QH-QP-11
6.6.《外发加工掌握程序》 QH-QP-10
6.7.《采购掌握程序》 QH-QP-08
6.8.《物料吸收程序》 QH-QP-14
6.9.《记录掌握程序》 QH-QP-02
6.10.《进料考验程序》 QH-QP-18
7.管理体系记录
7.4.《生产操持表》
7.5.《生产非常联结单》
7.6.《日排程操持》
7.7.《物料操持单》
7.8.《请购单》
7.9.《采购单》
7.10.《成品入库单》
7.11.《套料需求操持表》