新生产系统的设计和履行常日是耗时且高本钱的过程,完成设计、采购、安装后,在移交生产运行之前还须要一个阶段,即调试阶段。如果在开拓过程中的任何地方涌现了缺点而没有被创造,那么每个开拓阶段的缺点本钱将大大增加,未检测到的缺点可能会在调试期间造成设备重大的破坏。
数字孪生对履行过程的前中后进行容错冲销,将大部分的操作-除了末了安装之外全部移到虚拟层,设计、开拓、调试等事情都是虚拟层进行,得到最优和最确定的方案后有相称的把握再上线利用。
随着工艺哀求和掌握繁芜度的增加,使得本来就很棘手的设备调试变得更加棘手,分开了现场运行环境,机器、电气部件和自动化软件就得不到充分的调试,设备设计的精确性和有效性等得不到有效的保障。在调试阶段,工程师会创造缺点,修正设计,编写和优化程序,以及对操作职员进行新设备、新操作流程培训。
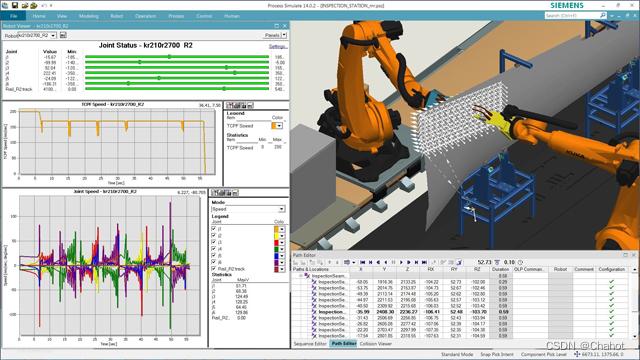
工艺设计和虚拟调试,特殊适宜一些禁止远程调试的业务场景。实在这些事情很多供应商也干过,只不过未必是数字孪生罢了:仿照安装环境啊,而且还不是局部仿照,是全局仿照。当然有条件的设备供应商可以自己仿照一个小型环境,如果本钱太高,也可以用数字孪生来仿照一个虚拟的调试和安装环境。通过现实的运行机理导入数据和流程到数字孪生,这里我们再超前一点:数字孪生能不能搞用户化和通用化呢,当然也可以。
这个阶段是难以操持,会延迟生产,也会造成本钱超支,并可能导致延迟发货,影响客户满意度。由于数字孪生是物理资产的准确表征,可以用于对新网络或设备设计的虚拟调试。
在虚拟调试时,如果创造问题须要进行设计优化,则可以在打算机上对虚拟的系统模型进行变动,虚拟调试许可重新变动网络方案、重新编程机器人或更改变频驱动器、PLC 编程等操作。一旦重新编程,系统会再次进行测试,如果通过,则可以进行下一阶段的物理支配。
通过虚拟调试实现对设备的设计进行仿真验证,缩短从设计到物理实现的韶光;
利用虚拟调试来提前测试设备运动部件以创造机器干涉,以及提前验证自动化 PLC 编程和上位软件,这样可以使现场的调试速率更快,风险更低。
2.系统框架
网络方案和仿真验证系统
在设计阶段,通过 SINETPLAN 实现对工业网络 PROFINET 的方案设计和仿真,识别潜在的问题并避免发生。
新建、组态 PROFINET 网络,或导入现有项目,进行网络负载仿真,流量整形担保网络运行安全可靠,优化网络资源和透明化网络利用率;也可以对已安装 PROFINET 网络进行在线扫描和验证。
网络架构让真正网络工程师去搞,我不懂。知道它是啥就行,不用什么都通,面面俱到:知道须要什么,输出什么,标准是什么,流程是什么差不多了,再合营合营嘛。
设备的数字孪生
在设备开拓中运用虚拟调试,首先要创建一个设备的数字孪生即虚拟设备,虚拟设备构成紧张有三部分,即物理和运动系统模型、电气和行为模型、自动化模型。
个中:
物理和运动系统模型紧张是机器组件,比如设备主体、实行机构、运送带、工装夹具等;
电气和行为模型紧张是一些活动组件例如驱动器、阀门和外设行为;
自动化模型是 DCS,PLC 程序和上位机软件。
这三种模型都须要数字孪生仿真
虚拟调试系统(这个东西是核心,其他都是赞助)
虚拟调试系统分软件在环(SiL: Software in Loop)和硬件在环 (HiL:Hardware in Loop),根据不同的仿真环境可以选择软件在环或硬件在环。
软件在环是把整体设备完备虚拟化,即由虚拟掌握器 CPU、虚拟 HMI、虚拟旗子暗记及模型算法、虚拟机器模型组成;
(软件在环便是软件虚拟化,仿真化,不仅仿真软件模型,贴张图说这个便是HMI视图也可以,还要仿真的软件的功能)
硬件在环是把设备紧张的硬件放在仿真环境中,利用真实 HMI、真实掌握器 CPU、现场 IO 设备与虚拟机器模型组成虚拟设备模型。
(硬件在环是将现实的硬件设备和虚拟硬件设备仿真模型连接起来,共同组成一个硬件仿真环境,无论是软件也好,硬件也好,终极都是仿真实体的模型和机理,就这两件事,看清楚了就不以为繁芜了。)
通过搭建虚拟调试平台,对包含多物理场以及常日存在于机电一体化产品中的自动化干系行为进行 3D 建模和仿真,使机器、电气和自动化设计能够同时事情,并行协同设计一个项目:
a)对工业网络 PROFINET 进行高效方案、布局、仿真和验证。(网络方案)
b)机器工程师可以根据三维形状和运动学创建数字模型。(实体数字模型,前面的根本知识篇中有这些观点,感兴趣的小伙伴可以去看一下)
c)电气工程师可以选择并定位传感器和驱动器等行为模型。(行为模型仿真,别忘了还有上一篇里面提及的动作掌握柜,什么事理呢,所有干系的物理性操作的集成封装到一个掌握系统中)
d)自动化编程职员可以设计设备的掌握逻辑和 HMI 程序,然后与机器模型、电气模型连接,实现基于事宜或命令的掌握和运动模型。
(视图交互模型,没有这个称不上数字孪生,最多算个仿真剖析程序)
3.案例特点
虚拟调试不同于在物理天下中调试新网络或设备,而是通过在虚拟天下中创建数字孪生,然后仿照新网络或设备的功能测试和模型验证,这样可以实现:
a)方案-仿真-测试
b)虚拟环境中的程序代码测试和调试
c)设备运行仿真,可以创造设计问题以及对办理方案的快速评估
d)机器人单元操作的仿真
e)仿真新设备的产能,识别空间限定和对现有操作的影响,以便在安装前办理这些问题
f)对设备操作职员的培训
4.履行步骤
对PFOFINET工业网络的方案、仿真与测试,通过三步即可达到目的,包括创建/加载项目、调度、剖析并输出报告。
对设备的虚拟调试,须要以下几个紧张步骤:
1)建立虚拟设备模型
首先要理解设备的真实掌握机理,剖析每个运动的真实物理场景中
所对应的掌握旗子暗记,在 NX MCD 建立虚拟设备模型,创建及匹配相应的旗子暗记,并利用旗子暗记来掌握运动模型的动作,仿真实际机器部件的运动情形,
为后续利用 PLC 的虚拟调试做根本。
2)建立虚拟掌握系统
在 TIA Portal 中编写 PLC 掌握程序和 HMI 画面,编程和 HMI 事情完成后,启动 PLCSIM Advanced 建立虚拟 PLC,与真实 PLC 具有相同的功能,将 PLC 掌握程序下载到虚拟 PLC 中;并启动 HMI 人机界面仿真器建立虚拟 HMI 人机界面。
3)建立虚拟模型与虚拟掌握系统的映射关系
将 PLC 中的输入、输出变量与 NX MCD 中输入、输出旗子暗记建立联系,从而达到 PLC 中的输出旗子暗记作为 NX MCD 的输入旗子暗记,反之 PLC 中输入旗子暗记作为 NX MCD 的输出旗子暗记。
4)通过虚拟调试试验验证设计的可用性
启动虚拟 PLC,在线监控 PLC 掌握程序的运行情形;在 NX MCD 中运行虚拟设备模型,查见地式掌握的运动情形。通过虚拟设备模型的运动和掌握逻辑仿真,优化改进自动化模型、电气和行为模型,以及物料和运动模型,而不会造成硬件资源的摧残浪费蹂躏。
这个流程解释我们昨天扯的还是比较精确的,数字孪生怎么实现:先用传统的办法把流程走出来,然后用数字孪生的技能进行赋能。这也是个人比较建议的一种办法。MES的系统怎么实现,先用数据采集去完成数据完全性效验,在此根本上对着需求和MES的框架或核心功能去构建。说白了,便是在数据的根本上用MES的理论和框架进行赋能。ERP也是一样的道理。什么意思呢?先用传统的办法把全体业务流程理清楚了,把数据准备好了,末了再此根本上用数字化进行赋能。什么是系统:主体便是数据和业务流程,其他都是做事。这20%搞定了也就平衡了80%的系统需求。为什么要搞用户化和通用化,便是这个缘故原由。
5.核心技能
软件在环仿真技能
软件在环(SiL: Software in Loop)仿真是采取虚拟掌握器模型和虚拟工具模型连接起形成闭环,以运行仿真工具来仿照其运行行为和状态,可以完成一些实际中难于实现的场景测试。
(由于软件本身便是半虚拟的,实在说白了便是在数字孪生的场景中把软件的功能集成进来,就这么个事情。比如网络监测软件,是检测网络通信本身的状态,或者网络电缆的检测软件-探伤功能,这些都可以集成进来)
硬件在环 (HiL: Hardware in Loop) 仿真是将实时处理器和虚拟工具结合起来运行仿真模型来仿照仿真工具的运行行为和状态,通过 I/O、OPCUA 及网络等接口与被测工具相连接。也称为半实物仿真,是将须要仿真的部分系统硬件直接放到仿真回路中的仿真系统,仿真时,实际系统的一部分设备与打算机通过各种信息通道相连,打算机和实际硬件共同完成仿真事情,并将仿真结果在电脑中进行剖析,从而判断硬件的运行情形。
(硬件的仿真便是虚实结合,实现实际设备和虚拟模型的敛收速率同步,实在便是状态和运行机理同步。数字孪生搞什么?模型状态和运行机理啊。)
硬件在环仿真不仅填补了纯数字仿真中的许多毛病,提高了全体模型的置信度,而且可以大大减轻编程的事情量。这种仿真的另一个上风在于它实现了仿真模型和实际系统间的实时数据交互,使仿真结果的验证过程非常直不雅观,大大缩短了产品开拓周期。
6.案例成效和意义
工业网络和设备的设计过程很难预测莅临盆和利用过程会不会涌现问题,而虚拟调试带来许多好处之一便是验证工业网络和设备设计的可行性。
虚拟调试许可设计者在物理设备生产之提高行任何修正和优化,由于用户在测试过程中可以修复缺点,及时对自动化系统或机器设计进行改进优化,可以节省韶光。虚拟调试将每个设计细节都验证好之后,就可以把这台设备做出来,然后只要在物理设备上再做 15%或者 20%这样少量的软件优化,设备就可以正常运行。
通过数字孪生技能的运用,帮助企业在实际投入物理工具(如设备、生产线)之前即能在虚拟环境中进行设计、方案、优化、仿真、测试、掩护与预测等,在实际的生产运营过程中同步优化全体生产流程,以明珞装备为例,通过虚拟调试系统在方案、设计和调试阶段与客户交流数据和折衷,将项目周期缩短了 20%-30%,减少 50% 以上的工程现场调试韶光,终极实现高效的柔性生产,提高企业核心竞争力。通过对 PROFINET 的方案与仿真,实现调试前的透明化,节约本钱,变被动为主动。