杨文杰 王霞 王荣 邵荣昌
(天水华天科技株式会社 甘肃天水)
择要:
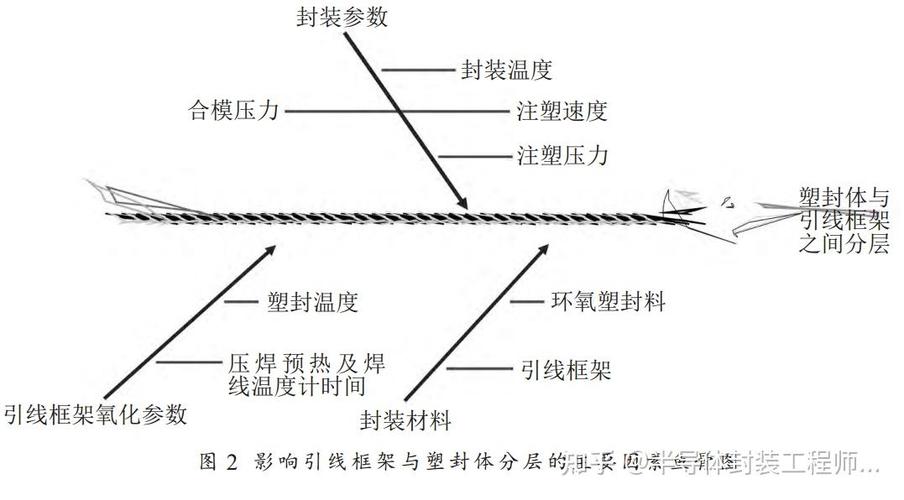
在现行引线框架的IC封装模式过程中,分层是一种重大的质量非常征象,且是产品本身可靠性的绝对关键成分。而在生产过程中如何防患于未然,提高合格率,是急需办理的问题。概述分层及分层分类,提出影响分层的紧张成分,并给出了避免塑封器件分层的有效方法,降落产品失落效的几率,提高可靠性。
塑封器件在利用的过程中,在本钱上具备很大的上风。随着集成电路集成度的持续增长,为了知足电子器件微型化、多功能化和智能化的哀求,半导体分立器件越来越小,器件表面积减小,引线框架设计的高密度化,给产能带来新的机遇。但也产生了一系列的问题:
(1)封装体因尺寸减小而引起机器强度的降落;
(2)无铅化进程哀求回流焊的温度提高,这使得塑封料须要提高自身的粘结强度以抵御因回流焊温度升高引起的塑封料与芯片之间以及塑封料与引线框架之间的分层征象;
(3)塑封材料与框架之间的热膨胀系数不一致,在温度变革较大时引起的分层征象等。
1分层概述
在塑封器的利用过程中,由于利用不同的参数,因此造身分歧材料的粘结面存在着分离或者剥离征象,属于内应力问题的一种,会影响塑封器件的事情与利用寿命。分层紧张是由于材料不同,从而湿气与热应力对其造成毁坏。对框架式的塑封元器件中,分层存在大概4种形态[1],如图1所示。
分层的4种形态:
(1)芯片与塑封体间的分层。紧张是由于芯片表面污染造成与塑封料之间的结合力低落,现在在封装前,一样平常会用去离子水对其表面进行洗濯,去除芯片表面的污染物,达到预防的目的。
(2)引线键合区分层。一样平常为引脚在成型时受到拉扯时产生的变形或者框架本身的品质非常造成的。
(3)芯片与镀层之间的分层。这种征象设备在粘片时,粘接面分层,紧张是镀层(银/铜)分布不屈均、设备的稳定性或镀层的品质不好造成的。
(4)框架与塑封体之间的分层。框架氧化是缘故原由之一,但是无法确认在封装后是否一定会产生,纵然经由等离子洗濯,仍旧无法避免其发生。
2分层分类剖析
塑封成型的毛病种类很多,在不同的封装形式上有不同的表现形式,发生的几率和位置也有很大的差异,产生的缘故原由也比较繁芜,并且相互牵连,相互影响,以是须要综合剖析,制订出相应的行之有效的办理方法。很多器件失落效机制一样平常表现为两大类:一是热应力毁坏,二是湿气毁坏[2]。
2.1热应力毁坏
在温度循环及高温下,由于塑封料与不同材料(芯片、引线框架、金丝)热膨胀系数的差异,封装体内局部应力集中。当应力水平超过封装材料的屈从强度时,就会引发失落效,对器件密封性也有着不可忽略的影响。环氧塑封材料的热膨胀系数和杨氏模量在玻璃化温度(Tg)附近对温度的变革非常敏感,温度一旦发生变革,环氧塑封料的热膨胀系数和杨氏模量就会发生较明显的变革。若部分器件的事情温度可能会靠近玻璃化温度,这样的事情环境更随意马虎使器件涌现分层的失落效征象。
2.2湿气毁坏
环氧树脂是非致密性的,湿气渗入器件紧张有两条路子:
(1)通过塑封料包封层本体;
(2)通过塑封料包封层与引线框架间的间隙。
当湿气通过这两条路子到达芯片表面时,在其表面形成一层导电水膜,并将塑封估中的Na+、CL-离子也随之带入,在电位差的作为下,加速了对芯片表面布线的电化学堕落,终极导致电路内引线开路。随着电路集成度的不断提高,布线越来越细,因此,布线堕落对器件寿命的影响就加倍严重。在分立器件生产过程中电镀这一环节,电镀液中含有较多的离子,一旦这些离子浸入塑封里内部,很随意马虎造成芯片表面堕落,乃至是分层。
3分层紧张成分剖析及改进方案
如图1所示,分层紧张为4种表现形式,本文紧张以引线框架与塑封体之间的分层为代表进行剖析。
首先,列出影响引线框架与塑封体间分层紧张成分包括a.引线框架,b.材料,c.封装参数。构成鱼骨图,如图2所示。依鱼骨图逐一找出可能影响分层的各成分。
3.1塑封参数对分层的影响
3.1.1封装温度
生产过程中,模具温度掌握在略高于塑封料玻璃化温度Tg时,能得到较空想的流动性,约160℃~180℃。模具温度过高,塑封料固化过快,内应力增大,包封层与框架粘接力低落。同时,固化过快也会使模具冲不满。模具温度过低,塑封料流动性差,同样会涌现模具添补不良,包封层机器强度低落。同时,保持模具各区域温度均匀是非常主要的,由于模具温度不屈均,会造成塑封料固化程度不屈均,导致器件机器强度不一致。
3.1.2注塑压力
注塑压力的选择,要根据塑封料的流动性和模具温度而定,压力过小,器件包封层密度低,与框架黏结性差,易发生吸湿堕落,并涌现模具没有注满塑封料提前固化的情形;压力过大,对内引线冲击力增大,造成内引线被冲歪或冲断,并可能涌现溢料,堵塞出气孔,产生气泡和添补不良。
3.1.3注模速率
注塑速率的选择紧张根据塑封料的凝胶化韶光确定。凝胶化韶光短,注模速率要稍快,反之亦然。注模要在凝胶化韶光结束前完成,否则由于塑封料的提前固化造成内引线冲断或包封层毛病。
3.1.4合模压力
合模压力的选择紧张根据压痕的深浅以及溢料情形。
塑封工艺调度的同时,还应把稳到预成型料块的保管、模具的洗濯、环境的温湿度等缘故原由对塑封工序的影响。
3.2塑封材料对分层的影响:
之前谈论过,湿气可通过塑封料包封层进入内部,或通过塑封料包封层与金属框架间的间隙。当湿气通过这两条路子到达芯片表面时,在其表面形成一层导电水膜,并将塑封估中的Na+、CL-离子也随之带入,在电位差的作为下,加速了对芯片表面铝布线的电化学堕落,终极导致电路内引线开路。针对上述问题,我们必须哀求:塑封料要有较高的纯度,Na+、CL离子降至最低;塑封料的紧张身分:环氧树脂与无机填料的结合力要高,以阻挡湿气由本体的渗入;塑封料与框架金属要有较好的粘接性;芯片表面的钝化层要尽可能地完善,其对湿气也有很好的屏蔽浸染。
由于塑封料、芯片、金属框架的线膨胀系数不匹配而产生的内应力,对器件密封性有着不可忽略的影响。由于塑封料膨胀系数(20-26E-6/℃)比芯片、框架(-16E-6/℃)的较大,在注模成型冷却或在器件利用环境的温差较大时,有可能导致压焊点脱开,焊线断裂乃至包封层与框架粘接处分开,由此而引起其器件失落效。由此可见,塑封料的线膨胀系数应尽可能的低,但这个降落是受到限定的,由于在降落应力的同时,塑封料的热导率也随之降落,这对付封装大功率的器件十分不利,要使这两个方面得以兼顾,取决于配方中填料的类型和用量。
3.3引线框架氧化对分层的影响
引线框架是电子封装中最紧张的构造材料,在封装体中可以起到固定芯片、保护内部元件、分配电旗子暗记的浸染,同时还供应散热通道。但是金属铜具备较强的亲氧性,在封装工艺加热的过程中随意马虎发生氧化,形成氧化膜。金属的表面氧化会改变原性子,而化学性子的改变也连带使物理性子产生变革,如表面湿润、表面张力以及结合力。研究创造[4],引线框架表面氧化状况对塑封料的粘接强度有较大影响,其氧化膜认为是塑封料封装再回流焊工艺等分层及裂纹的紧张缘故原由之一[5]。
在封装工艺中存在加热可能造成引线框架氧化的工艺包括以下几个方面:(1)芯片粘贴后的烘烤;(2)压焊前的预热;(3)引线键合时的加热,虽然有氮气流保护,但引线框架还是存在一定的氧化;(4)引线框架的预热,EMC注塑成型前必须对引线框架进行预热,担保其良好的粘接,但其间并没有保护性气氛,预热韶光只能靠人工掌握,由于给料须要较永劫光,极易造成引线框的严重氧化。铜氧化层有两种不同机制产生[5]:(1)在室温中,一个薄膜层的氧化亚铜(Cu2O)由氧化还原反应,成型于铜基材的表面。其反应式为:
4Cu+2H2O→Cu2O+4H+4e在阳极
O2+2H2O+4e→4(OH)在阴极
氧化亚铜(Cu2O)产生在铜材质的最表面,经由大量的Cu离子及电子间传输而形成。氧化亚铜在空气中是呈现不稳定状态,且会很快的转换为氧化铜(CuO),并借由氧的扩散效应而缓慢发展。而另一机制为氧化铜(CuO)与EMC的结合力会比氧化亚铜来的弱,此为产生分层的可能成分。而引线框架在不同温度与韶光下受热,其与塑封体间的结合强度如图3所示。
传统不雅观点认为,引线框架氧化膜的形成会降落铜与环氧树脂的粘接强度,引起裂纹,因此为了提高封装的可靠性,应只管即便避免框架的氧化或去除氧化。但是一些学者进行的研究表明,具有一定厚度的氧化膜可以提高粘接强度。在此方面,有一定的分期存在。Mino,Tosbikazu等人认为[6],氧化膜厚度只有在一定数值下,才能担保框架与EMC的粘接强度,通过一贯氧化膜成长的方法,可以避免粘接强度的降落。
3.4去溢料的影响对分层的影响
造身分层的主因与塑封料黏度、框架工艺有直接关系,但去毛刺溶液对付分层有一定的毁坏浸染,而在如何避免去毛刺溶液对付分层影响方面:
(1)药水利用温度的影响,由于材料之间弹性系数的差异,受热胀冷缩影响对付分层有明显影响,这就哀求药水要朝着低温趋势发展;
(2)去毛刺药水中须要选用分子量大的组分,减少渗透力对付塑封料造成的影响。
(3)只管即便避免去毛刺溶液对纳米级氧化亚铜层的毁坏力,产品在塑封前引线框架表面形成纳米级氧化亚铜,有利于增强塑封料与框架之间的结合力,药水毁坏这层氧化亚铜层进而影响分层。
(4)从药水的反应动力学角度考虑,去毛刺溶液应考虑组分对付溢料溶解溶胀的力度不易过大。
4结论
综上所述,分层是一个综合性课题,须要事情职员对各个工序的工艺,利用材料进行调度,优化、提高塑封的可靠性,以扩大塑封的引用范围,进一步提高塑封集成电路的发展。