——写给车间的维修管理辅导材料
一、要始终贯彻事前预防重于事后维修的思想
新的一轮TPM推进已经1年零8个月了,这个阶段中,至少我们明白了一个道理,那便是预防比救火主要。各车间维修管理,应始终坚持以预防故障为主,事前重于事后的理念,把维修事情重点精力放到预防性作业上来。
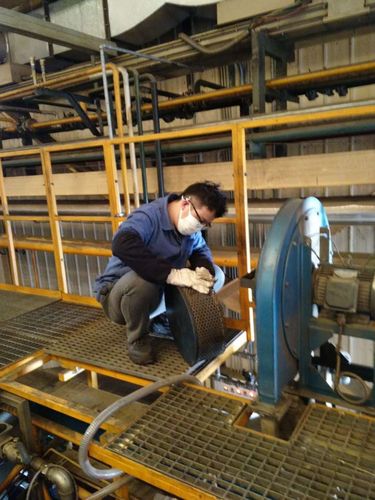
维修作业与工序作业不同,它有长期性、持续性、繁芜性的特点。如果没有持续的坚持,就不会有成效。
正由于如此,要做好维修管理,必须做到“三个有”:
1、有目标:设备能力的坚持和改进,是个循规蹈矩的过程,因此各阶段都要有目标。
这个目标传统上只环绕设备可动率展开。目前,我们逐步勾引由可动率单一目标过渡到可动率、本钱和职员能力三个目标。这样可以更好地辅导维修管理的方向,反响公司和工厂发展中的需求。我们推举这三个指标逐步作为对工厂(车间)考察的公司级一级指标。
我们可以环绕这三个指标进行指标链分解,天生二级指标,如环绕可动率的检修操持实行率、故障方法整改率、设备无缺率、点检实行率等。这些指标按照我们目前的想法,是封闭在车间内部,由车间直接考察工段和班组。
***常常讲“零目标”,比如零毛病、零故障、零摧残浪费蹂躏,我们的目标中,敢不敢寻衅这些“零”呢?
2、有操持:正是由于维修管理须要持续性的坚持,以是才要有操持。
要督匆匆维修工段环绕目标制订操持,把二级指标落实到操持中,并公示出来。目前最大的问题,便是很多工段没有一个明确的操持,事情随着生产走,随着故障走。
我们该当有长期、中期目标和操持,并根据这些操持分解为短期可实行操持。
3、有标准:标准化可谓是做好维修事情的一个诀窍,以是这样说,是由于维修的繁芜性决定的。
“繁芜的事情大略化,大略化的事情标准化,标准化的事情持续化。”这是来自丰田体系的一句名言。维修看着繁芜,但只要我们坚持做好标准化,就会把它做大略,做持久。
维修的标准有什么?这些标准便是作业办法书、设备管理基准书、点检基准、保养基准、操作规程、润滑图表等这些我们常日所说的“机台文件”。各车间一定要从日常故障、维修作业中去不断积累和完善这些标准,并结合这些标准去培训职员,才能在沉淀中,不断把事情做得越来越好。
二、维修详细该当做什么?
这个问题,大家或许都会说我们做了这么多年,维修该干什么怎么会不知道?实在不然,现在我们所做好的,该当只是冰山一角。
从故障形成机制来讲,我们要做的事情无非一是在故障前,一是在故障后。
而故障前,又要按照两种情形来对待:
针对逼迫劣化:我们知道,逼迫劣化是指设备利用、保养不当造成的劣化。比如违章操作、润滑不良、灰尘、水气等环境成分造成的设备早期磨损,这些“逼迫劣化”的成分,都是可以预防的。目前我们的对策便是针对微毛病的操作工人自主保全,和针对繁芜毛病的维修工的专业点检。
针对自然劣化:自然劣化取决于零部件的质量和寿命,属于自然磨损,是无法避免的,但可以通过定期定量保全来提前采纳对策。
故障后,我们要做的也同样有两个方向:
规复:在最短韶光内处理故障,恢复活产。同时,研究如何快速修复同类故障,通过作业办法书和培训来展开。
防止复发:便是研究对策,防止同样的故障再次发生。
目前我们的大多数事情都环绕故障后展开,而且也做不到位。故障前预防的架子是都有了,但形式化的东西太多,更多是为了检讨和贯标。
下面的图形比较完全地表达了维修到底该干什么,我们看看自己的车间到底开展了多少?
图1:维修都要有哪些作业?
维修日常作业,无非要做好这样几件事:
1、故障维修及管理
发生故障后,要沿着两个方向来管理故障:
方向1:修睦故障:
首先是尽快规复,这个过程须要“高手”,也正是太多的故障培养了许多真正的“高手”。但这些“高手”的背后,是公司背负的丢失。
能不能把大家都培养成高手?这就要坐下来,针对发生过的,修理韶光长的故障,研究快速修复的方法。然后体例出《故障维修作业办法书》,再通过单点课(OPL)培训教给所有维修工。
有一个指标叫“均匀故障规复韶光”,便是来源于此。
方向2:防止复发:
我们提出过所谓防止故障再发的“四要素”,便是:
1)真因剖析:通过《故障剖析报告》、剖析会等形式,找到故障发生的真因,特殊针对零部件的重大故障,一定要做“失落效模式剖析”。
2)毛病改进:故障复发一定来源于毛病,如果没有缺陷就不会复发。因此,故障剖析找到真因后,一定要针对毛病通过针对性修理操持组织改进。
3)横向展开:我们也叫“他机点检”。便是针对同类设备或构造,反思是否有相同的毛病,如果有,就要一并处理和改进。
4)标准化:防止故障的真正最可靠的方法,便是把处理已发故障的对策标准化。如创造毛病,可以关照专业科做标准化来在未来采购中防止毛病;我们还可以修正点检基准、设备管理基准书、定期定量保全操持、作业办法书等来掌握和减少故障的发生。
这4个要素,比较精准地描述了防止故障再发生的方法。
一工厂涂装车间在这方面有许多积累,在故障管理和掌握方面有自己的特色和履历,他们的“零停台活动”小组和“八步事情法”值得大家借鉴。
2、预防性作业
按照前面的故障形成机制,我们方案和支配了如下预防性维修作业,体例了辅导性流程和表单。
1)针对逼迫劣化的日常点检
为什么要做点检?实在便是要通过维修职员的日常巡回检讨,来动态创造设备毛病,节制设备运行状态。为此,我们哀求针对所有设备体例《设备点检基准卡》,维修工根据《基准卡》来检讨设备,并做记录。
点检不但是检讨,还包括对创造的问题,能当时处理的要立即处理,不能立即处理的,体例到节假日针对性修理操持里来履行。
现在的问题是,我们许多维修工的点检,只是拿着笔在记录上去画圈。我们反复强调维修工一定要佩带工具,试问,如果连工具都不带,如何开展设备检讨?如何及时处理毛病和不良?又如何能防止故障发生?如果把点检做成画圈,不如不做。建议车间不妨检讨一下,我们车间是不是有“画圈点检”,有多少人真正地在负责点检?
我们推举过车间要做好“三级确认”,班长每天、工段每周、主任不定期确认,才能真正担保点检做到实处。
2)针对自然劣化的年度预防维修操持(定期定量保全)
从2011年开始,我们废除了传统苏联式的年度操持。缘故原由是苏联式的操持没有针对详细设备的作业标准,表单太多,缺少针对性,及工时定额不再适应现在设备繁芜性大幅度提高的实际情形。
去年四季度,我们支配了师承丰田体系的定期定量保全,并以此代替传统的年度操持。
为什么要做定期定量保全操持?个别车间因不理解而未开展,实在,这是我们目前唯一对应设备自然劣化的预防性对策。如果不做,就会发生重大的突发故障,并影响产品质量。
我们的定期定量保全,推举大家做定期紧固(如夹具、定位)、定期润滑(换油、注油)、定期调度(如吊具、滑撬)、定期检讨(把握不了改换周期或没必要定期改换的点)、定期改换(轴承、皮带、接头、夹紧块、打仗器等周期规律明显的易损件)、定期备份(程序、数据)、定期检测(如导轨、链条)、定期校准(如传感器)等。大家看看,这些如果不做,积累下来,是不是会诱发重大故障,是不是会影响产品质量?
希望至今还没有开展的车间,尽快把这项事情开展起来。二工厂涂装车间在这方面投入了许多的精力,只管维修职员不大理解,但车间还是强力进行了推动。他们的老维修职员讲:希望多做点有技能的活,实在,相对付故障修理讲,预防保全便是很大略。
3)针对性修理
针对性修理操持的来源大致有:点检创造的不能及时处理的毛病、故障规复后的改进、年度操持分解、大中修项目、设备改造、设备日常保养等。
由此我们可以创造,针对性修理也是一种预防操持,只是随机性强些,相称部分来源于动态创造的问题和毛病。
大家都知道维修职员加班多,加班实在便是来自针对性操持,但我们可以通过预防维修作业,来逐步压缩随机发生的问题,进而逐步减少针对性操持,减少加班。
如何做好预防保全,我们发布过《定期定量保全管理规定》、《设备工装点检管理规定》两个三级文件,大家可以参照。
3、自主维修
自主维修是TPM的主要支柱。为什么要做自主维修,缘故原由是要通过利用设备的操作工人精确利用设备,并通过自主点检和保养,把设备的眇小毛病掌握住,以免形成为大毛病。这是抑制故障发生的第一道门槛,如果真的演化成了大毛病,就须要维修工来办理。另一个缘故原由,也是现在我们的设备越来越多,维修职员,特殊是有技能的维修职员越来越少,要都靠维修职员来完成这些“芝麻”作业是不现实的。
实在自主保全就好比我们开车,爱护点开,掸掸灰,打扫一下车内卫生,听听发动机是否非常,看看胎压是否够,检讨一下是否缺机油、防冻液,这些我们都能负责去做,缘故原由是由于车是自己的。
大家常常不理解,认为操作工为什么要管维修,实在按照上面比喻就明白了。由于操作职员是直策应用者,设备的毛病和故障,大部分实在都是在他们手中逐步形成的。一个好的司机,车可以开百万公里无大修,一个好的操作者,也同样可以让设备少发生故障。这便是要做自主维修,既要精确操作设备,又要学会自主保全,还要学会改进,这我们也叫做“一人三技”。公司“多技能工”的提法,就源于这个思想。
MAZDA把自主维修一共分为7个步骤,从初期清扫开始,做到末了一步,可能要五年以上。这须要永劫光的坚持,自主维修的最高境界,便是变“要我做”,为“我要做”。
还有,说说清擦的问题。许多人讲,***就不清擦。实在,大部分故障都始于灰尘,由于灰尘一旦进入摩擦副,会造成摩擦副的快速磨损,几十倍地减少零部件的寿命。***部分地不擦设备,一是由于生产压力大,二是由于设备摩擦副防护比我们好得多。如果污染会磨损设备的敏感部位,他们比谁都擦得负责。我们的设备大部分都是低廉的价格买来的,更看重的是工艺能力,防护等级普遍比较低。
多数车间认为清擦便是擦灰,实在不然,清擦要做三样事情:一是擦净污染,二是肃清污染源和改进防护,三是同时点检设备毛病。一厂焊装车间很早就有一句话:“清扫便是检讨”,解释他们对清扫的理解比较到位。
三、维修工的培训与评价
从2009年11月我们提交的第一个报告开始,我们在公司多次提到维修工是核心技能工种,目前这种提法已经取得公司的认同。缘故原由是,维修工要节制的技能很繁芜,工种培训周期长、投入多,一个好的维修工,纵然是大中专和职业学校毕业,没有两三年的个人努力和公司培养,也很难“成手”。这点和工序工大略培训后可以上岗形成了光鲜比拟。
以是我们常常向公司提,维修工该当作为“资源”来保护,人事上要有分外的管理政策,只管即便不该用临时工,担保维修军队的稳定性。而且由于社会资源远远不能知足公司发展的须要,维修工的培养也要有提前量。
车间管理好维修工,要做两件事:
一是要积极开展培训,建立自己的造血能力。
车间的培训,可以以单点课为主,这种“十分钟”、“单课题”、“化整为零”的培训,可以见缝插针,适宜在生产的夹空里提升技能。当然利用安歇韶光做系统的根本培训也很主要。
培训素材从哪里来?那便是我们强调的《作业办法书》。故障维修、点检作业、修理作业中,凡是比较繁芜的过程,都可以体例《作业办法书》,要鼓励维修职员每个人都编写,作为车间的知识沉淀。这些办法书经由转化,便是OPL教材。几年下来,这些办法书可以有几百、上千份。《作业办法书》是车间维修最好的知识积累和继续办法。
一厂总装车间从03年就开始体例造业办法书,现在哀求维修班组每周做一次OPL培训,如果不做,就要在奖金中考察。试想,如果坚持下来,每个人一年都能学到50项以上的“点技能”,那是多大的收成?如果能坚持下去,维修工会个个都成为“高手”。
设备举动步伐科哀求外网维修职员每人每周写一份作业办法书,对快速提升新工人的技能也发挥了重大浸染。
二是评价,通过评价发挥维修职员的自觉性。
维修职员的评价比较繁芜,MAZDA和丰田把维修职员能节制的设备类型、台数都拿出来评,并利用雷达图的方法来校阅阅兵班组职员能力的均匀度。TFTM对维修工的评价紧张表示在劳动态度、开动率水平、个人技能三个方面,我们可以参考。
维修工要做那么多的事,不象操作工,生产线一转就必须随着转,维修工更多地靠自觉性,没有评价的勉励,是很难做到的。
现在以人事部和技能部为主导,正在方案和培植公司层面的维修职员培训和评价体系,在不久的将来,会全面推出。
四、维修根本管理:
车间维修的根本管理相称主要,情由是有太多的东西须要整理、积累,它们都是做好维修的主要支撑。
1、目视板
以前我们总以为,目视板是用来展示的,是花架子;现在我们创造,目视板是最好的管理工具。
维修工段该当有目视板,通过目视板,可以让车间领导、技能职员、维修管理职员,乃至每个维修工,都知道阶段目标、操持履行情形、故障移动曲线、本钱情形、故障或停台记录、毛病记录、项目情形、作业记录、毛病整改情形、培训课程、职员评价等等,可以上板的东西太多太多。日常动态更新的目视板是监督和管理好维修,整理管理思路,公开各种信息的最佳工具。
一厂总装车间的目视板值得推介,缘故原由是他们的目视板紧密结合维修管理的流程,所有的表单都是对事情的支持,没有一张是为了贴出来参不雅观的,而都是为了支撑事情的。建议大家去看看。
那些只为展览的目视板,不要也罢。
2、日常行为管理
前面说过,维修工更须要自觉性,由于他们和生产线的同步性关联并失慎密,大多数作业都是要自觉安排进行的。而他们要做的事却很多,而且都很繁芜。
我们考虑到维修的专业性,才建议各车间设置维修工段,并设置段长和TPM专项。前者紧张管理职员、操持和作业,后者管理我们这里罗嗦这么多的啰嗦业务的标准化、方法推进,特殊要推进自主维修。但还须要和公司干系部门折衷,争取他们的理解。
维修职员的日常行为须要有一个工段来管理,但管什么?不但是管考勤,更主要的是管维修职员的安全作业,监工具、劳保用品配备,管作业行为的自觉性,管维修操持的按时保质完成。
没有一个自觉的军队,不能调动他们的积极性,要做好车间维修事情,真的很难。
“要我做”是压出来的,“我要做”是带出来的。
3、技能管理
新版体系文件,把技能管理写进去了,这是维修下车间必须做的。技能管理做什么?便是网络、整理、归类各种用于支持维修的信息、资料,这些是车间维修的最大财富。这些东西包括:
a) 车间自己的图纸资料库。
b) 机台文件,这是车间技能管理的核心部分。包括操作规程、设备管理基准书、点检基准卡、润滑图表、保养基准等。
c) 检修操持,包括年度定期定量保全操持、针对性修理操持,毛病整改操持,项目操持等。
d) 记录。车间作业须要的记录有故障/停歇记录、点检作业记录、定期定量保全记录、毛病整改记录等。
e) 备件档案,即备件台帐、易损件清单、国产化方法、修旧利废等资料。
f) 故障剖析及报告。
g) 作业办法书、OPL教材、培训记录等。
h) 程序/数据备份。
i) 设备帐簿/档案。
j) 安装、调试记录。
实在,只要我们把稳,可以积累的东西可能还有很多。车间要为维修工段创造条件,我们说维修工段要有电脑,要有资料柜,要有阵地,便是由于维修须要管理和积累的东西很多。
二工厂就很有预见性,从设备安装调试时开始,工厂领导就督匆匆各车间做好维修的技能管理事情,当时他们叫“设备档案”。
五、不同环境、阶段的不同对策
各车间在推进TPM时,不同程度碰着过困惑。
实在,我们反对大略地照搬国外的“前辈履历”,大家齐步走,整洁划一地做TPM的某一步。管理的精髓,是把别人好的东西,结合自己的特点,找到适宜自己的方法。
下面的描述或许能解答大家的部分迷惑。
1、是否要成立保全班或中班?
保全班或中班是学自丰田体系的做法。基本想法是,把预防性作业拿出来,由一伙专门职员去做。这是由于预防性作业和生产操持的关联度不大的特点决定的,可以这样来组织。
我们都知道维修有“聚堆征象”,一旦涌现问题,真正办理问题的是少数人,后面每每围着一堆人在看热闹或打下手。我们何不把这些“打下手”的,技能相对弱些的职员调出来,专门去做预防维修。我们的老维修工不是说想要多做点有技能的事情吗?那就让他们多去做故障维修和培训,让修故障比较弱,但动手能力可能比较强的人(包括车间普遍反应浸染不大的那些新工人)来做保全。这样可以充分发挥维修职员的资源。
我们可以把维修作业分成自主维修——专业预防维修——故障维修/在线点检几个等级,分别由操作工人、中班(不倒班)、维修班来做。这样的组合,能发挥职员的最大效率。当然,为照顾个人发展,也可以阶段性地进行职员对流。
TFTM西青工厂,基本消灭了节假日加班检修,而且开动率保持很高,就和中班在发挥巨大浸染有关。
当然,我们不是每个车间都可以成立中班,要根据车间的详细情形和班制来安排。一厂总装、冲压、二厂焊装、涂装都成立了类似性子的班组。
2、各车间如何捉住维修的中央任务
各车间有不同的情形,维修事情重点不应该也不可能相同。如焊装车间设备多、夹具多、电极多,必须重视操作工人的自主维修;故障高发期间(如一厂涂装曾经的经历和二厂涂装),应侧重故障的管理,逐步过渡到预防性作业;开动率高的车间,一定要重视预防性维修,否则随着设备的逐步磨损,故障就会逐渐增多(如一、二厂总装)。
3、不同特色设备的不同策略
不同的设备,维修策略不应该完备相同。紧张有:
1)不同主要程度的设备。我们可以把设备按主要、一样平常主要、不主要分成A、B、C级。A类设备要多投入,安排点检、定期定量保全,并做好预案;B类可以开展点检和定期定量保全;C类只做一样平常性点检。
2)不同类型的设备。不同类的设备维修对策、周期等可能不同。如变电间、特种设备更要把稳安全运行;机器扮装备要更关注易损件状态和磨损;检测线、加液设备要关注传感器校准等。
3)不同服役阶段和状态不同的设备。不同服役阶段,磨损程度不同的设备,对策也不同。如状态好的,作业周期可以长些,检讨内容少些;状态差的,就要短些,检讨内容多些。
4)不同生产压力、职员压力的对策。职员多、生产容许的情形下,我们的作业周期可以安排短些,做得勤些,但生产压力大、职员少时,就要多关注重点部位。
我们以是说机台文件要掩护,各种检修标准不是一体例完了,就一成不变,便是这个道理。
以上罗嗦了这么多,缘故原由便是维修管理本来便是一件非常繁芜的事。感谢车间一贯以来,对技能部TPM推进的大力支持,这一年多,我们至少取得了不雅观念上的转变,车间领导也越来越成为维修管理的专家,来自丰田体系的各位领导也带给我们更多好的方法和履历,维修体系也逐步得到公司和各部门的重视。写这份资料的目的,也是阶段性地帮车间总结一下思路,希望公司的设备管理水平逐步走上更高的台阶,支撑公司的发展。