识别风险,肃清断点。随着科研飞机、发动机型号的增多,134厂新研产品逐年增多,且产品的研制交付周期不断缩短,C、S型新品的交付压力及难度逐步增加。为加快新品研制进度,有效管控新品研制过程中的各个环节,确保科研产品定时交付率,2018年,134厂将产品研制过程中的方案评审、设计评审、工艺评审、零件生产、装置试验等各个环节进行分解、细化,对各个环节的需求及风险点分别进行识别,整理形成了《产品实现策划矩阵表》《产品生产需求矩阵表》《产品研制试验需求矩阵表》(简称“三张表”)。在产品研制初期,对运行过程中的科研节点进行识别,形成事情项,并应对规避个中风险,促进了设计、工艺、生产的并行协同事情。通过“三张表”的运用,肃清了研制过程中的大部分“断点”,缩短了产品研制周期,通过科研例会平台,对项目进展情形进行检讨、通报,及时识别项目结束或涌现新的风险,纠正并制订办理方法,确保问题、风险“快速处理”。新品研制的过程更加“流畅”, 更加“精益”。自2018年3月“三张表”利用以来,134厂已顺利完成20余项新品的交付事情,新品定时交付率大幅提升,运用效果良好。
需求导向,系统保障。以精益生产为目标,134厂逐步建立起覆盖条约、需求、操持、落成、库存、交付、考察生产主过程管理线的生产管控平台,以信息化手段来支撑生产业务流程,打通了产品从订单到考察的主业务链,实现了生产操持的统一和闭环管理,奠定了134厂生产信息化根本, 提升了生产业务能力。通过优化生产操持管理业务,减少缺件、提高配套率、使操持逐渐合理;改变了过去操持职员手工体例操持的传统办法,平台系统的数据得到及时的更新,更便于及时、准确节制生产进度及库存资源状况;操持员与生产调度职员能及时折衷沟通,问题可以得到快速创造与处理;库存管理手段得到显著提升,打算机管理取代手工电子台账管理,配套效率高;避免了摧残浪费蹂躏,降落了本钱、缩短了生产交付周期;业务流程固化、管理更加透明化,生产环节状态更明晰。通过系统履行以及与人力资源、财务、密集柜系统的集成,初步打通了生产的业务数据流,对库存资源进行整合,实现数据信息共享。
目标拖动,细化管控。为了担保生产交付的及时性,134厂制订了科学合理的操持管理体系,从年度操持、月度操持、周操持、细化到逐日操持, 班组日操持表、日事情操持点检表等。在生产主制车间全面实行“日操持, 周管控”的模式,结合月度滚动操持、厂级分层例会等办法,统一各单位生产节拍,提升成品齐套率。生产单位同时利用“原材料备料操持、生产准备操持、日操持”“三驾马车齐拉动”。建立问题快速相应机制,实施看板拉动,在生产现场设置问题快速相应看板,对生产作业信息进行可视化展现, 结合非常问题看板,确保生产过程可控。利用分层例会对现场待办理问题落实时间节点,强力推进。以目标为导向,每周对操持实行进行管控,创造并办理问题。
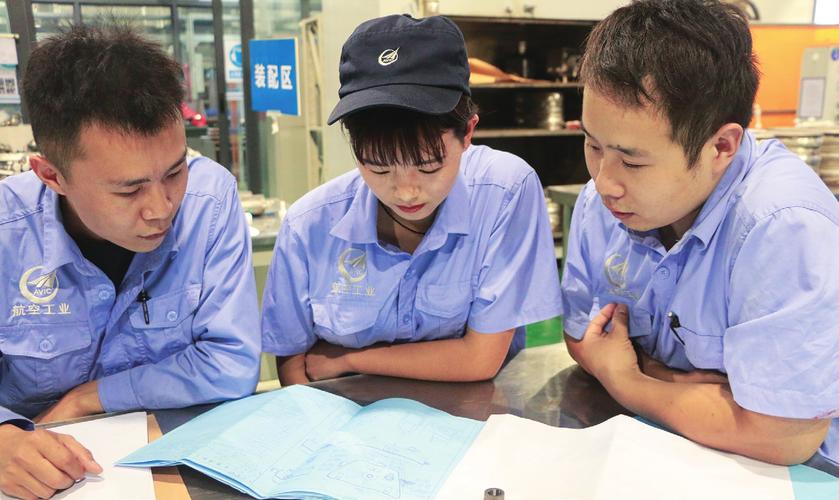
优化流程,初显成效。在车间生产经营中,工艺、操持、经管方面的数据本是相通的,但由于短缺联动, 形成了各式各样的版本,无法合理调配资源,造成了大量多余事情的摧残浪费蹂躏。2018年, 随着信息化的推进, 标准数据的编码从无到有,实现了工装工具、设备、职员的统一化管理,彻底肃清依赖纸质账本管理的混乱的弊端。MES系统的开拓运用,完备代替了传统纸质文件人力通报的模式,实现流程的升级优化,从备料、下料,到工装工具准备共计减少了8个流程。实现了信息流程的高效通报,杜绝了过程摧残浪费蹂躏。通过完善文件管理制度及考察,助力信息化的推进,冲破了工艺、操持、生产数据管理的孤岛,在车间建立起一个信息化的生产制造实行体系,稳定车间管理体系。
车间数字化单元最先起步,现已实现单元所有成产任务的线上运行, 选型产品已经实现订单、操持、准备、生产、数据采集、非常、剖析、考验、合格入库的全部业务流程利用, 并增加扩型操持33项。生产周期缩短120%以上,MES的运用为虎傅翼, 通过工装工具扫码出库、单元长扫码派工、员工扫码报工、考验扫码确认, 一系列的流程线上衔接有序,彻底改变了传统模式,减少了信息通报的无效环节,增加了操持可实行性,肃清了生产过程的断点,打通了车间生产业务链条,为实行134厂信息化,迈出了坚实的一步。