经由多年的履历积累总结出以下不良毛病:
注塑不满、凹陷、熔合缝、料流纹、光泽不好、气孔、黑点、溢边、翘曲变形、脱模不好、云彩、流道断裂、唱片沟纹、光环、麻点气、烧焦、冷料、喷射纹、银纹、飞边、须状斑纹、表面剥离、气泡、变色、空洞、波纹、模垢、拉丝、裂纹、浇口切割不良、主流道粘模、流涎、流线等
以上毛病成因:模具温度,流道温度,注射速率、注射压力,保压力、位置,保压韶光,转换点,锁模力、冷却韶光,炮筒温度、烤料温度、塑化速率,开锁模速率,背压等。
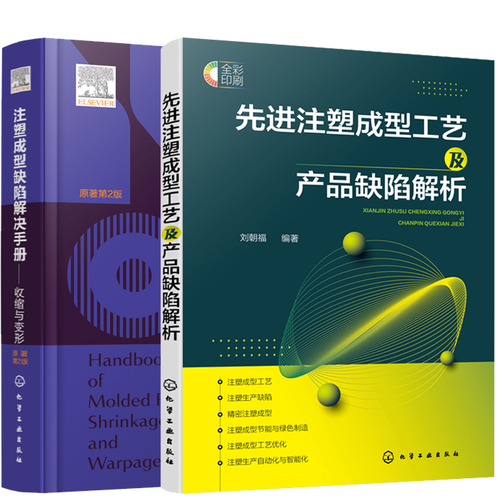
注塑成型各种毛病的征象及办理方法
(一)熔接痕(Weldline)熔接痕是由于来自不同方向的熔融树脂前端部分被冷却、在结合处未能完备领悟而产生的。熔合涌如今树脂合流之处。两股树脂流相遇时便会涌现熔合。此时,两者的温度越低,熔合就越明显。由于熔合处的两股树脂流并不会相互稠浊(由于在喷流中一边半固化一边提高),因此如果温度偏低,表层就会变厚,纹路很明显,而且强度也会降落。这是由于两者的粘协力变弱所致。相反,如果两股树脂流的温度较高,粘协力便会增强,外不雅观也就变得不很明显。在熔合处,两种熔化了的树脂受到挤压,此处的粘合状况取决于施加在该处的压力。保压越低,熔合就越明显,强度也就越低。如果不仅要考虑保压的设定,而且要考虑实际施加在熔合处的压力会降落这一条件,则上述(i)~(iv)都险些同样适用。这是由于随着固化的进行,压力通报会变得更加困难。此外,如果浇口尺寸变小,浇口位置变差的话,则熔合的外不雅观和强度都会恶化。熔合是树脂的合流点,同时也可能是流动末端。此时,如果不在该位置很好地设置一个排气口来排出气体,则会使熔合的外不雅观和强度恶化。
一样平常情形下,紧张影响外不雅观,对涂装、电镀产生影响。严重时,对制品强度产生影响
(特殊是在纤维增强树脂时,尤为严重)。可参考以下几项予以改进:
l)调度成型条件,提高流动性。如,提高树脂温度、提高模具温度、提高注射压力及速
度等。
2)增设排气槽,在熔接痕的产生处设置推出杆也有利于排气。
3)只管即便减少脱模剂的利用。
4)设置工艺溢料并作为熔接痕的产生处,成型后再予以割断去除。
5)若仅影响外不雅观,则可改变烧四位置,以改变熔接痕的位置。或者将熔接痕产生的部位处理为暗光泽面等,予以润色。
(二)放射纹
放射纹(Jetting)
1、表不雅观从浇口喷射出,有灰黯色的一股熔流在轻微打仗模壁后立时被随后注入的熔料包住。此毛病可能部分或完备隐蔽在制品内部。
物理缘故原由
放射纹每每发生在当熔料进入到模腔内,流体前端停滞发展的方向。它常常发生在大模腔的模具内,熔流没有直接打仗到模壁或没有碰着障碍。通过浇口后,有些热的熔料打仗到相对较冷的模腔表面后冷却,在充模过程中不能同随后的熔料紧密结合在一起。
撤除明显的表面毛病,放射纹伴随不屈均性,熔料产生冻结拉伸,残余应力和冷应变而产生,这些成分都影响产品质量。
在多数情形下不太可能只通过调节成型参数改进,只有改进浇口位置和几何形状尺寸才可以避免。
与加工参数有关的缘故原由与改良方法见下表:
1、注射速率太快降落注射速率
2、注射速率单级采取多级注射速率:慢-快
3、熔料温度太低提高料筒温度(对热敏性材料只在计量区)。增加低螺杆背压
与设计有关的缘故原由与改良方法见下表:
1、浇口和模壁之间过渡不好供应圆弧过渡
2、浇口太小增加浇口
3、浇口位于截面厚度的中央浇口复位位,采取障碍注射
工艺溢料是指用手工在模具上开一条深一些的排气槽,在生产时此槽产生出来的(批峰),又叫工艺批峰,紧张是用来改进烧胶或熔接痕,可将烧胶或熔接痕调度到此批峰上,生产后将其切除。
2、烧四位置是指将烧胶或熔接痕用工艺调到不用随意马虎看到的位置,以免应响产品的外不雅观。
3、增加低螺杆背压是指调度背压
4、障碍注射是指在入水前方加一挡块。改变射胶浇口流向位置。以改变射胶时胶料的流动方向。这种方法对付办理喷射纹有帮助。
(三)灰黑斑纹(Greyor black clouding)
1、表不雅观灰黑斑纹可能发生在浇口附近,流道的中间和阔别浇口的部分。只能在透明的零件中可看出,并且每每用PMMA,PC和PS料制成的产品有此征象。
物理缘故原由
如果计量过程开始太早,螺杆喂料区里颗粒裹入的空气没有溢出喂料口,空气就会被挤入熔料内。然而,喂料区内的压力太低不能将空气移到后面。料筒内熔估中被挤入的空气就会使制品内产生灰黑斑纹。
就像压缩点火式柴油发动机里面所发生的情形一样,被料筒内挤入的空气所造成的焦化征象有时被称为“柴油机效应”。
焦化征象可阐明熔料和挤入的气泡交卸的地方由于压缩浸染产生高温,同时空气内的氧气通过氧化浸染使熔料产生断裂。
工艺调试该当在喂料区的中间开始熔化过程,此处熔料压力已较高,迫使颗粒之间的空气朝后移动并溢出料口。
与加工参数有关的缘故原由与改良方法见下表:
1、螺杆背压太低增加螺杆背压
2、喂料区的料筒温度过高低降喂料区的料筒温度
3、螺杆转速过快降落螺杆转速
4、循环韶光短,即熔料在料筒内残留韶光短延长循环韶光
与设计有关的缘故原由与改良方法见下表:
1、不合理的螺杆几何形状选用加料段长的螺杆,且加料段的螺槽较深
要弄清楚是水斑还是其它斑纹,还有水斑不一定把胶料烘干透就不会产生,其它因子也会型成有水斑征象、例如模具冻水过冻、由于温差效应产生露水、模具混水湛流、材料殽杂等都会产生此征象。
(四)料头附近有暗区(Dullareas nearsprue)
1、表不雅观在料头周围有可辨别的环形—如利用中央式浇口则为中央圆,如利用侧浇口则为同心圆,这是由于环形尺寸小,看上去像黯晕。这紧张是加工高粘性(低流动性)材料时会发生这种征象,如PC、PMMA和ABS等。
物理缘故原由
如果注射速率太高,熔料流动速度过快且粘性高,料头附近表层部分材料随意马虎被错位和渗入。这些错位就会在外层显现出黯晕。
在料头附近,流动速率特殊高,然后逐步降落,随着注射速率变为常数,流动体前端扩展为一个逐渐加宽的圆形。同时在料头附近为得到低的流体前流速率,必须采取多级注射,例如:慢—较快—快。目的是在全体充模循环种得到均一的熔体前流速率。
常日以为黯晕是在保压阶段熔料错位而产生的。实际上,前流效应的浸染是在保压阶段将熔料移入了制品内部。
与加工参数有关的缘故原由与改良方法见下表:
1、流速太高采取多级注射:慢-较快-快
2、熔料温度太低增加料筒温度,增加螺杆背压
3、模壁温度太低增加模壁温度
与设计有关的缘故原由与改良方法见下表:
1、浇口与制品成锐角在浇口和制品间成弧形
2、浇口直径太小增加浇口直径
3、浇口位置缺点浇口重新定位
(五)空隙(Void)
1、表不雅观
制品内部的空隙表现为圆形或拉长的气泡形式。仅仅是透明的制品才可以从表面看出里面的空隙;不透明的制品无法从表面测出。空隙每每发生在壁相对较厚的制品内并且是在最厚的地方。
物理缘故原由
当制品内有泡产生时,常常认为是气泡,是模具内的空气被流入模腔的熔料裹入。另一个阐明是料筒内的水气和气泡会费尽心机进入到制品的内部。以是说,这样的“泡”的产生有多方面的根源。
一开始,生产的制品会形成一层坚硬的外皮,并且视模具冷却的程度往里或快或慢的发展。然而在厚壁区域里,中央部分仍连续保持较永劫光的粘性。外皮有足够强度抵抗任何应力紧缩。结果,里面的熔料被往外拉长,在制品内仍为塑性的中央部分形成空隙与加工参数有关的缘故原由与改良方法见下表:
1、保压太低提高保压压力
2、保压韶光太短提高保压韶光
3、模壁温度太低提高模壁温度
4、熔料温度太高低降熔体温度
与设计有关的缘故原由与改良方法见下表:
1、浇口横截面太小增加浇口横截面,缩短浇道
2、喷嘴孔太小增大喷嘴孔
3、浇口开在薄壁区浇口开在厚壁区
(六)白点(GranulesUnmelted)
1、表不雅观料头附近有未熔化的颗粒。对薄壁制品来说是不可能得到光滑的表面。
物理缘故原由
由于薄壁制品生产成型周期短,因此必须以很高的螺杆转速进行塑化从而使熔料在螺杆料筒内残留韶光缩短。在碰到薄壁制品生产时,常日包括PE、PP,PC等,模具工会试着降落熔料温度以缩短冷却韶光,未完备熔化的颗粒会被注射进模具内。
与加工参数有关的缘故原由与改良方法见下表:
1、熔料温度太低增加料筒温度
2、螺杆转速太高低降螺杆转速
3、螺杆背压太低增加螺杆背压
4、循环韶光短,即熔料在料筒内残留韶光短延长循环韶光
与设计有关的缘故原由与改良方法见下表:
1、不合理的螺杆几何形状选用适当几何形状的螺杆(含计量切变区)
(七)颜色不均(Colourstreaks)
表不雅观颜色不均是制品表面的颜色不一样,可在料头附近和远处,偶尔也会在锐边的料流区涌现。
物理缘故原由
颜色不均是由于颜料分配不均而造成的,尤其是通过色母、色粉或液态色料加色时。
在温度低于推举的加工温度情形下,母料或色料不能完备均匀化。当成型温度过高,或料筒的残留韶光太长,也随意马虎造成颜料或塑料的热降解,导致颜色不均。
当材料在精确的温度下进行塑化或均化时,如果通过料头横截面时注射太快,可能会产生摩擦热造成颜料的降解和颜色的改变。
常日在利用色母料时,应确保颜料及其溶解液需上色的树脂在化学、物理特性方面的兼容性。
与加工参数有关的缘故原由与改良方法见下表:
1、材料未均匀稠浊降落螺杆速率;增加料筒温度,增加螺杆背压
2、熔料温度太低增加料筒温度,增加螺杆背压
3、螺杆背压太低增加螺杆背压
4、螺杆速率太高减少螺杆速率
与设计有关的缘故原由与改良方法见下表:
1、螺杆行程过长用直径较大或长径比较大的料筒
2、熔料在料筒内勾留韶光短用直径较大或长径比较大的料筒
3、螺杆L:D太低利用长径比较大的料筒
4、螺杆压缩比低采取高压缩比螺杆
5、没有剪切段和稠浊段供应剪切段和(或)稠浊段
(八)料头附近有灰黑斑(Diesel effect away from sprue)
1、表不雅观制品表面上以浇口或附近一点为中央向外发散涌现银色或玄色纹迹。如果利用低粘性(高流动性)材料和高成型温度,纹路大多是玄色,如果采取高粘性(低流动性)材料,纹路大多是银白色。
物理缘故原由
这是由被挤入和压缩的另一种气泡。如果螺杆降压幅度太高(螺杆回缩),降压速度过快,螺杆头前面的熔料开释太多,会在熔料内产生负压,在熔料温度太高的情形下,很随意马虎在熔料内形成气泡。
这些气泡会在往后的注射阶段再次受到压缩,导致玄色纹路在制品内天生,终极成为“柴油机效应”。
如果浇口为中央式浇口,纹路就会从料头向外辐射。在带热流道注射的情形下,纹路只会再某段流道往后涌现,由于在热流道里的材料不包含任何气泡,因而材料不会产生烧焦的痕迹。只有再料筒头的熔料才会产生烧焦的痕迹。
如果是低粘性的熔料,纹路比高粘性材料更灰黯和更大,由于前者再螺杆降压过程中随意马虎产生真空和空隙。
3、与加工参数有关的缘故原由与改良方法见下表:
1、螺杆降压太高减小螺杆降压幅度
2、螺杆降压率太高减小螺杆降压率
3、熔料温度太高低降料筒温度,降落螺杆背压,降落螺杆转速
(九)水迹纹(Moisturestreaks)
表不雅观水迹纹是在制品表面有很长的银丝,水迹纹的开口方向沿着料流方向。在制品未完备充满的地方,流体前端很粗糙。
物理缘故原由
一些塑料如PA、ABS、PMMA、SAN和PBT等随意马虎吸水。如果塑料储藏条件不好,潮气就会进入颗粒或附在表面。当颗粒熔化时,潮气会转变成蒸汽形成气泡。在注射期间,这些气泡会暴露在流体前锋的表面,爆裂然后产生不规则的纹路
与加工参数有关的缘故原由与改良方法见下表:
1、颗粒内残留的水分太高检讨颗粒的储藏条件,缩短颗粒在料斗内的韶光,给材料供应足够的预烘干
(十)唱片纹(Gramophonerippie)
1、表不雅观在全体料流方向上乃至到流道末端可以看出很深的槽。在采取高粘性(流动性差)材料和厚壁的制品生产时涌现这种征象,这些槽看上去象唱片上的纹路。在PC料做成的产品上非常清晰,但在ABS制品上更大,并且呈灰黯色。
物理缘故原由
如果在注射过程中,特殊时在低注射速率的条件下,打仗模具表面的熔体凝集速率太快,流动阻力太高,就会在流体前端产生扭曲。凝固的外层材料不会完备打仗模腔壁而形成波浪状。这些波浪状的材料会冻结,保压也不再能够将它们弄平整。
与加工参数有关的缘故原由与改良方法见下表:
1、注射速率太低增加注射速率
2、熔料温度太低提高料筒温度,增加螺杆背压
3、模具表面温度太低增加模具温度
4、保压太低增加保压
与设计有关的缘故原由与改良方法见下表:
1、浇口横截面太小增加浇口横截面,缩短浇道
2、喷嘴孔太小增大喷嘴孔
(十一)冷料头(Coldslug)
(1)何谓冷料?
(2)冷料的天生缘故原由
・喷嘴温度偏低
(3)冷料的对策
・提高喷嘴温度
・检讨排气口
・使机筒每个周期退却撤退一次
(1) 何谓冷料?
1、冷料是指在喷头前端处固化的树脂混入成型品的征象。
2、冷料在成型品表面表现为光泽不好或喷射纹。虽然看起来相似,3、但由于对策不同,因此须要把稳。
(2) 冷料的天生缘故原由
(2-1) 喷嘴温度偏低
于成型品的喷嘴前端部分,为了防止流涎(树脂从喷嘴前真个孔中流出的征象),一样平常要适当降落树脂温度。因此,注射到模具中的树脂的最初部分会变成固化或半固化树脂。这被称为冷料。
为防止树脂进入模腔,一样平常在模具一侧的主流道根部及分流道等处制作树脂积存器以作为冷料的吸收留器。但是,如果树脂温度过低,冷料的量便会增多,从而有可能进入模腔。这些会呈现出喷射纹或光泽不好状外不雅观。
(3) 冷料的对策
(3-1) 提高喷嘴温度
防止冷料,提高喷嘴温度是很有效的。但必须兼顾流涎的涌现. 为了不产生流涎,应逐渐提高机筒和喷嘴的设定温度。如果因此喷嘴固定于模具的办法成型,则提高模具温度也是很有效果的
(3-2) 扩大冷料阱(树脂积存处)
扩大冷料阱可防止冷料进入成形品内。一样平常建议利用长度为主流道根部直径1.5倍旁边的冷料阱。
(3-3) 使机筒每个周期退却撤退一次
喷嘴固定于模具的办法成型的情形下,使机筒每个周期退却撤退一次并使喷嘴从模具中脱出也是一个很有效的方法。但也必须把稳流涎。由于流涎还取决于树脂的粘度和流动性、喷嘴型号以及孔径,因此自己必须反复进行实际试验(包括上述温度调度在内)。根据情形,还应预先考虑通过降落喷嘴孔径(即改用别的喷嘴)来抑制流涎以及相应地提高温度来抑制冷料等方法。
1、表不雅观这指的是有一块冷料卡在或粘在料头附近的表面上。冷料头会导致制品表面涌现痕迹,严重的还会降落制品的力学性能
物理缘故原由
当熔料可以在机器喷嘴或热流道附近冷却时每每会产生冷料头。由于先注射进的熔料总是聚拢在浇口附近,在此区域就会产生毛病。它的成因是由于机器喷嘴或热流道喷嘴周围的温度掌握不合理。
3、与加工参数有关的缘故原由与改良方法见下表:
1、热流道温度太低增加热流道温度
2、喷嘴温度太低丈量喷嘴温度,提高喷嘴温度,减少喷嘴 打仗区
4、与设计有关的缘故原由与改良方法见下表:
1、喷嘴横截面太小增加喷嘴横截面
2、浇口几何尺寸不合理改变浇口几何尺寸将冷料头留在通 道
3、热流道几何尺寸不合理改变热流道喷嘴几何尺寸
(十二)顶白(Ejectormarks)
表不雅观在制品面对喷嘴一侧,即在顶出杆位于模具顶出一侧的地方创造应力泛白和应力升高的征象
物理缘故原由
如果必须的脱模力太高或顶出杆的表面相对较小,此处的表面压力会很高,发生变形终极造成顶出部位泛白。
与加工参数有关的缘故原由与改良方法见下表:
1、保压太高低降保压
2、保压韶光太长缩短保压韶光
3、保压韶光切换太迟将保压切换提前
4、冷却韶光太短延长冷却韶光
与设计有关的缘故原由与改良方法见下表:
1、脱模斜度不足按规格选择脱模斜度
2、脱模方向上表面粗糙对脱模方向上模具进行抛光
3、顶出一侧上形成真空型芯内装气阀
(十三)翘曲(变形、波折、扭曲)
由于塑料成型时流动方向的紧缩率比垂直方向的大,使制件各向紧缩率不同而翘曲,又由于注射充模时不可避免地在制件内部残留有较大的内应力而引起翘曲,这些都是高应力取向造成的变形的表现。以是从根本上说,模具设计决定了制件的翘曲方向,要通过变更成型条件来抑制这种方向是十分困难的,终极办理问题必须从模具设计和改良动手。
剖析如下:
1.模具方面:
(1)制件的厚度、质量要均匀。
(2)冷却系统的设计要使模具型腔各部分温度均匀,浇注系统要使料流对称避免因流动方向、紧缩率不同而造成翘曲,适当加粗较难成型部份的分流道、主流道,只管即便肃清型腔内的密度差、压力差、温度差。
(3)制件厚薄的过渡区及转角要足够调皮,要有良好的脱模性,如增加脱模余度,改进模面的抛光,顶出系统要保持平衡。
(4)排气要良好。
(5)增加制件壁厚或增加抗翘曲方向,由加强筋来增强制件抗翘曲能力。
(6)模具所用的材料强度不敷。
2.塑料方面:
结晶型比非结晶型塑料涌现的翘曲变形机会多,加之结晶型塑料可利用结晶度随冷却速率增大而降落,紧缩率变小的结晶过程来纠正翘曲变形。
3.加工方面:
(1)注射压力太高,保压韶光太长,熔料温度太低速率太快会造成内应力增加而涌现翘曲变形。
(2)模具温度过高,冷却韶光过短,使脱模时的制件过热而涌现顶出变形。
(3)在保持最低限度充料量下减少螺杆转速和背压降落密度来限定内应力的产生。
(4)必要时可对随意马虎翘曲变形的制件进行模具软性定形或脱模后进行退米处理。
(5)注射、保压韶光:原则上设定为浇口封闭韶光。如果注射、保压韶光比浇口封闭韶光短,对模腔充分通报并保持压力的保压工程就会不敷,有时会产生变形。
冷却韶光:由于成型品在模腔内的形状保持韶光延长,以是许多场合下增加冷却韶光会减少变形。但对付某些形状则相反,因模具(模芯)的报紧等缘故原由,有时增加冷却韶光会造成脱模不良而产生变形,故不能一概而论。
因此,设定冷却韶光时,需把稳成型品的顶出平衡、厚度及模具温度等问题。
模具温度:与冷却韶光同样,在成型品的形状保持效果方面,许多场合低落低模具温度会减少变形。但它也并非只要温度低即可。对付有些形状,温度低反而会导致模腔与模芯间的温度差增大而随意马虎产生变形。并且,模具温度低于成型品的利用环境温度时,因后紧缩会产生变形或尺寸变革等问题。
因此可以说,在模具温度方面,主要的不是温度高低而是包括模芯冷却在内的温度均匀(均衡),以实现均匀的成型紧缩。
(十四) 拉丝
(1)何谓拉丝
(2)拉丝的天生缘故原由
主流道前端尚未固化
材料和等级固有的问题
(3)拉丝的对策
使主流道前端固化
加快开模速率,增大开模量
变动喷嘴
(1) 何谓拉丝(外不雅观)
拉丝是指主流道前端没有断开而伸展成丝状的一种征象。最大的问题是有时会发生成形品因拉丝而无法脱落,最大的问题是有时会发生成形品因拉丝而无法脱落,被模具夹住,从而导致无法连续成形。
树脂的纺丝性(在熔融状态下拉伸时可伸长成丝状的性子)越好,拉丝就越严重。因此与改性材料比较,非强化的材料更易引起拉丝。 (2)拉丝的天生缘故原由
(2-1) 主流道前端尚未固化
注射后,经由冷却工序,主流道会与产品一起固化,但由于其前端与机筒喷嘴相接,从而保持着一定的温度,因此有时芯部并未完备固化。如果此时打开模具,纺丝性(拉伸时会伸展成丝状且不会断开)好的材料便随意马虎在主流道前端产生拉丝。
从成型条件来说,如果树脂温度(特殊是喷嘴温度)或模具温度偏高,则随意马虎引起拉丝。
(2-2) 材料和等级固有的问题
大家知道,液晶聚合物以及利用过某种弹性体的耐冲击性等级比其它材料更随意马虎引起拉丝。这是由于这些材料的纺丝性很好。此外,就同一种材料而言,粘度越低就越随意马虎拉丝。
(十五)色条、色线、色花这是采取色母粒着色的塑料制件较常涌现的问题,虽然色母粒着色在色型稳定性、色质纯度和颜色迁移性等方面均优于干粉着色、染浆着色,但分配性,亦即色粒在稀释塑料在稠浊均匀程度却相对较差,制成品自然就带
1)提高加料段温度,特殊是加料段后真个温度,使其温度靠近或略高于熔融段温度,使色母粒进入熔融段时尽快熔化,促进与稀释均匀稠浊,增加液态稠浊机会。
(2)在螺杆转速一定的情形下,增加背压压力使料筒内的熔料温度、剪切浸染都得到提高。
(3)修正模具,特殊浇注系统,如浇口过宽,融料通过时,紊流效果差,温度提升不高,于是就不屈均,色带模腔,应予改有区域性光荣差异。
(十六)成品黏膜(脱模困难)
是指成型品无法从模具中取出的一种征象。
依据成型品的尺寸及温度等条件,脱模阻力增大时就会产生脱模不良。虽然也会受到树脂特性和成型条件的影响,但最紧张的缘故原由仍在于成型品的形状和模具的构造。特殊须要把稳的是与苗条的加强筋、轮毂和塑孔栓抱紧相伴时的情形。
当塑孔栓等处周围的成型紧缩偏大时,对塑孔栓的抱紧力就会变大,从而随意马虎发生脱模不良。在成型条件方面,模具温度偏低且保压偏大时随意马虎引起脱模不良。
当长的加强筋或轮毂等直立的成型品中发生过添补时,这些加强筋或轮毂将变得难以脱落,从而造成脱模不良。在成型条件方面,模具温度偏低且保压偏大时随意马虎引起脱模不良。这一点与塑孔栓抱紧恰好相反。
模腔制品部的脱模斜度偏小时,由于脱模阻力偏大,因此随意马虎发生脱模不良。顶出针的位置也有很大影响(最好在脱模阻力偏大处设置顶出针)。此外,模腔表面的光洁度或损伤对脱模阻力也有影响,从而造成脱模不良。
在射出成型时,成品会有黏膜发生,首先要考虑射出压力或保压压力是否过高.射出压力太大会造成成品过度饱和,使塑料充压入其它的空隙中,致使成品卡在模穴里脱模困难,在取出时随意马虎有黏膜发生.
而当料管温度过高时,常日会涌现两种征象.一是温度过高使塑料受分解而变质,失落去它原有之特性;并在脱模过程中涌现破碎或撕裂,造成黏膜.二是胶料充填入模穴后不易冷却,需加长周期韶光,殊不合经济效益.以是需适度依胶料之特性调节其运作温度, 至于模具方面的问题,如果进料口不平衡,会使成品脱模时易有黏膜征象,这时就要在模具上作改进的方法,下表即为成品黏膜可能发生的缘故原由及处理对策:
故障缘故原由处理方法
(1) 填料过饱降落射出剂量、韶光及速率
(2)射出压力或料筒温度过高低降射出压力或料筒温度
(3)保压韶光太久减少保压韶光
(4)射出速率太快降落射出速率
(5)进料不均使部分过饱变更溢口大小或位置
(6)冷却韶光不敷增加冷却韶光
(7)模具温度过高或过低调度模温及两侧相对温度
(8)模具内有脱模倒角(undercut)修模具撤除倒角
(9)多穴模进料口不平衡,或单穴模各进料口不平衡限定塑料 的流程,尽可能靠近主流道
(10)探筒件脱模排气设计不良供应充分的逸气道
(11)螺杆提高韶光太长减少螺杆提高韶光
(12)模心错位调度模心,并利用「退拨」角锁紧之
(13) 模子表面过于粗糙打光模穴表面,喷脱模剂
4-3浇道黏模(脱模困难)
故障缘故原由处理方法
一、浇道过大修正模具
二、浇道冷却不足延长冷却韶光或降落料管温度
三、浇道脱模角不足修正模具增加角度
四、浇道凹弧与射嘴之合营不正重新调度与合营
五、浇道表里面不只或有脱模倒角检修模具
七、浇道外孔有破坏检修模具
八、无浇道抓锁加设抓锁
当因塑孔栓抱紧而造成的脱模阻力偏大时,通过提高保压和模具温度等来抑制成型紧缩的方法也很有效。
相反,如果因过添补而使尺寸增大并嵌入模腔内时,则应降落保压和模具温度等来增加成型紧缩量。当因塑孔栓抱紧而造成的脱模阻力偏大时,通过提高保压和模具温度等来抑制成型紧缩的方法也很有效。
增加模腔周边、轮毂以及加强筋等处的脱模斜度。特殊是在已经嵌牢的情形下,应通过添加顶出针等方法给须要增加顶出强度的部分配置顶出针。
(十七)包风(airtraps)
包风(air traps)是指:熔胶之前将模穴内的空气包覆,它发生在熔胶之前从不同方向的汇流,或是空气无法从排气孔或镶埋件之缝隙逃逸的情形下。包风常日发生在末了充填的区域,如果这些区域的排气孔太小或者没有排气孔,就会造成包风,使塑件内部产生空洞或气泡、塑件短射或是表面瑕疪。其余:塑件肉厚差异大时,熔胶方向于往厚区流动而造成竞流效应(race-tracking effect),这也是造成包风的紧张缘故原由,
要肃清包风可以降落射出速率,以改变充填模式;或者改变排气孔位置、加大排气孔尺寸。由于竞流效应所造的包风可以藉由改变塑件肉厚此例或改变排气孔位置加以改进排气问题。包风的改进方法解释如下:
(1) 变更塑件设计:缩减肉厚比例,可以减低熔胶的竞流效。
(2) 应变更模具设计:将排气孔设置在适当的位置就可以改进排气。排气孔常日设在末了充饱的区域,例如模具与模具交卸处、分模面、镶埋件与模壁之间、顶针及模具滑块的位置。重新设计浇口和熔胶传送系统可以改变充填模式,使末了充填区域落在适当的排气孔位置。此外,应确定有足够大的排气孔,足以让充填时的空气逃逸;但是也要小心排气孔不能太大而造成毛边。建议的排气孔尺寸,结晶性塑料为0.025厘米(0.001英吋),不定形塑料为0.038厘米(0.0015英吋)。
(3)调度成形条件:高射出速率会导致喷射流,造成包风。利用较低的射出速率可以让空气有充足的韶光逃逸。
(十八)起疮:(银色条纹)
成品表面,以CATE为中央,有很多银白色的条痕,基本上是顺着质料的流动方向产生。这种征象是许多不良条件累积后发生的,有时要捉住真正的缘故原由很困难。
1.1 原估中如果有水分或其它挥发身分,未充分烘干,则表面上就会产生很多银条。
1.2 原估中有时混入其它质料时,也会形成起疮,其形状呈云母状或针点状,随意马虎与其它缘故原由造成的起疮分别。
1.3 质料或料管不清洁时,也随意马虎发生这种情形。
1.4 射出韶光长,初期射入到模穴内的质料温度低,固化的结果,使挥发身分不会打消,尤其对温度敏感的质料,发常会涌现这种状况。
1.5 如果模温低,则质料固化快也随意马虎发生(1。4)之状况,使挥发身分不会排出除。
1.6 模具排气不良时,质料进入时气体不易打消,会产生起疮,像这种状况,成品顶部每每会烧黑。
1.7 模具上如果附着水分,则充填质料带来的热将其蒸发,与熔融的质料领悟,形成起疮,呈蛋白色雾状。
1.8 胶道冷料窝有冷料或者小,射出时,冷却的质料带入模穴内,一部分会迅速固化形成薄层,刚开始生产时模温低也会开成起疮。
1.9 质料在充填过程中,因模穴面打仗部分急冷形成薄层,又被后面的质料融化分解,形成白色或污痕状,多见于薄壳产品。
1.10 充填时,质料成乱流状能,使质料流径路线延长,并受模穴内构造的影响产生磨擦加之充填速率比质料冷却速率快,GATE位置处于筋骨处或者小随意马虎产生起疮,成品肉厚急剧化的地方也随意马虎产生起疮。
1.11 GATE以及流道小或变形,充填速率快,瞬间产生磨擦使温度急升造成质料分解。
1.12 原估中含有再生料,未充分烘干,射出时分解,则产生起疮。
1.13 质料在料管中勾留韶光久,造成部分过热分解。
1.14 背压不敷,卷入空气(压缩比不敷)。
起疮:表一
成
型
机
可塑化能力不敷。
树脂过热分解(料管温度)
料管内质料勾留久,造成部分过热。
射出压力过高。
螺杆卷入空气(背压不敷)。
模
具
模具内排气不良。
模具温度低。
胶道冷料窝存储小。
GATE 过小或变形。
模具表面有水分。
模穴的形状不良(横截面或壁厚变革较多较急)。
原
料
原估中由水分及挥发身分。
质料烘干不敷。
混入其它质料。
(十九)注塑件尺寸差异
1.注塑件毛病的特色
注塑过程中重量尺寸的变革超过了模具、注塑机、塑料组合的生产能力。
2.可能涌现问题的缘故原由
(1).输入射料缸内的塑料不均。
(2).射料缸温度或颠簸的范围太大。
(3).注塑机容量太小。
(4).注塑压力不稳定。
(5).螺杆复位不稳定。
(6).运作韶光的变革、溶液黏度不一致。
(7).注射速率(流量掌握)不稳定。
(8).利用了不适宜模具的塑料品种。
(9).考虑模温、注射压力、速率、韶光和保压
等对产品的影响。
3.补救方法
(1).检讨有无充足的冷却水流经料斗喉以保持精确的温度。
(2).检讨是否劣质或松脱的热电偶。
(3).检讨与温度掌握器一起利用的热电偶是否属于精确类型。
(4).检讨注塑机的注塑量和塑化能力,然后与实际注塑量和每小时的注
塑料用量进行比较。
(5).检讨是否每次运作都有稳定的熔融热料。
(6).检讨回流防止阀有否透露,若有须要就进行改换。
(7).检讨是否缺点的进料设定。
(8).担保螺杆在每次运作复回位置都是稳定的,即不多于0.4mm的变革。
(9).检讨运作韶光的不一致性。
(10).利用背压。
(11).检讨液压系统运作是否正常,油温是否过高或过低(25—60oC)。
(12).选择适宜模具的塑料品种(紧张从紧缩率及机器强度考虑)。
(13).重新调度全体生产工艺。
(二十)银纹(包括表面气泡和内部气孔)
造成毛病的紧张缘故原由是气体(紧张有水汽、分解气、溶剂气、空气)的滋扰。如果螺杆转速过快,背压偏低,则卷入正在塑化的树脂中的空宇量就会增多。其结果是成型品表面涌现条纹状气泡,并随意马虎形成银纹。树脂属于化学物质,因此会随着温度的增加而逐渐分解。树脂温度越高,分解就越多,银纹也就越随意马虎涌现。如果材料的预干燥不敷,水分和树脂中原有的气体身分就会被原封不动地带入成型品,从而随意马虎形成银纹。在气体没有完备排净的状态下,气泡就会残留在成型品表面,从而随意马虎涌现银纹。如果因洗濯不敷等缘故原由,导致与原来的树脂不同的身分混入,而且该树脂的温度的偏低,有时便会产生气体并诱发银纹。
1.机台方面:
(1)料筒、螺杆磨损或过胶头、过胶圈存在料流角,长期受热而分解。
(2)加热系统失落控,造成温度过高而分解,应检讨热电偶、发热圈等加热组件是否有问题。螺杆设计不当,造成个解或随意马虎带进空气。
2.模具方面:
(1)排气不良。
(2)模具中流道、浇口、型腔的磨擦阻力大,造成局部过热而涌现分解。
(3)浇口、型腔分布不平衡,冷却系统不合理都会造成受热不平衡而涌现局部过热或壅塞空气的信道。(4)冷却通路漏水进入型腔。
3.塑料方面:
(1)塑料湿度大,添加再生料比例过多或含有有害性屑料(屑料极易分解),应充分干燥塑料及肃清屑料。
(2)从大气中吸潮或从着色剂吸潮,应对着色剂也进行干燥,最好在机台上装干燥器。
(3)塑估中添加的润滑剂、稳定剂等的用量过多或稠浊不均,或者塑料本身带有挥发性溶剂。稠浊塑料受热程度难以兼顾时也会涌现分解。
(4)塑料受污染,混有其它塑料。
4.加工方面:
(1)设置温度、压力、速率、背压、熔胶马达转速过高造身分化,或压力、速度过低,注射韶光、保压不充分、背压过低时,由于未能得到高压而密度不敷无法溶化气体而涌现银纹,应设置适当的温度、压力、速率与韶光及采取多段注射速率。
(2)背压低、转速快易使空气进入料筒,随熔料进入模具,周期过永劫融料在料筒内受热过长而涌现分解。
(3)料量不敷,加料缓冲垫过大,料温太低或模温太低都影响料的流动和成型压力,匆匆赌气泡的天生。
气泡
根据气泡的产生缘故原由,办理的对策有以下几个方面:
1)在制品壁厚较大时,其外表面冷却速率比中央部的快,因此,随着冷却的进行,中央部的树脂边紧缩边向表面扩展,使中央部产生充填不敷。这种情形被称为真空气泡。办理方法紧张有:
a)根据壁厚,确定合理的浇口,浇道尺寸。一样平常浇口高度应为制品壁厚的50%~60%。
b)至浇口封合为止,留有一定的补充注射料。
C)注射韶光应较浇口封合时间略长。
d)降落注射速率,提高注射压力,
e)采取熔融粘度等级高的材料。
2)由于挥发性气体的产生而造成的气泡,办理的方法紧张有:
a)充分进行预干燥。
b)降落树脂温度,避免产生分解气体。
3)流动性差造成的气泡,可通过提高树脂及模具的温度、提高注射速率予以办理。
气泡(Gas bubbles)
1、表不雅观
制品表面和内部有许多气泡—紧张在料头附近。流道中途和阔别料头的地方—不仅是发生在制品壁厚的地方。气泡有着不同的尺寸和不同的形状。
物理缘故原由
气泡紧张发生在必须在高温下加工的热敏性材料。如果必须的成型温度太高,通过分子分裂而导致材料分解,熔料就有发生热降解的危险,成型过程中气泡就随意马虎产生。
如果周期韶光长,常日可能是太长的残留韶光和行程利用不敷的缘故原由。也可能由于料筒内的熔料过热。
与加工参数有关的缘故原由与改良方法见下表:
1、熔料温度太高低降料筒温度、螺杆背压和螺杆转速
2、熔料在料筒内残留韶光过长利用较小的料筒直径
与设计有关的缘故原由与改良方法见下表:
1、不合理的螺杆几何形状利用低压缩螺杆
(二十一)浇口区域毛病
1.光芒线
在垂直制件方向的点浇口设计中,注塑时制件表面涌现了以浇口为中央的由不同颜色深度和光泽组成的辐射系统,称为光芒线。大体有三种表现,即深色底暗色线,暗色底深色线及在浇口周围暗色线密而发白。这类毛病大多在注制聚苯乙烯与改性聚苯乙烯稠浊料时涌现,与下列成分有关:两种料在流变性、着色性等方面有差异,浇注系统平流层与紊流层流速和受热状况有差异;塑料因热分解而天生烧焦丝;塑料进模时气态物质的滋扰。
办理方法:
(1)采取稠浊塑料时,要稠浊好塑料,塑料的颗粒大小要相同与均匀。
(2)塑料和着色剂要稠浊均匀,必要时要加入适当分散剂,用机器稠浊。
(3)塑化要完备,机台的塑化性能要良好。
(4)降落注射压力与速率、缩短注射和保压韶光,同时提高模温,提高射嘴温度,同时减少前炉温度。
(5)防止塑料的降解而造成粘性增大的熔料及焦化物质:如把稳螺杆与料筒是否磨损而存在角,或加温系统失落控,加工操作不当造成塑料长期加热而分解。可以通过抛光螺杆和料筒前真个表里面。
(6)改进浇口设计,如放大浇口直径,改变浇口位置,将浇口改成圆角过渡,试对浇口进行局部加热,在流道端添加冷料井。
(二十二)紧缩凹陷
1.机台方面:
(1)射嘴孔太大造成融料回流而涌现紧缩,太小时阻力大料量不敷涌现紧缩。
(2)锁模力不敷造成飞边也会涌现紧缩,应检讨锁模系统是否有问题。
(3)塑化量不敷应选用塑化量大的机台,检讨螺杆与料筒是否磨损。
2.模具方面:
(1)制件设计要使壁厚均匀,担保紧缩同等。
(2)模具的冷却、加温系统要担保各部份的温度同等。(3)浇注系统要担保通畅,阻力不能过大,如主流道、分流道、浇口的尺寸要适当,光洁度要足够,过渡区要圆弧过渡。
(4)对薄件应提高温度,担保料流畅顺,对厚壁制件应降落模温。
(5)浇口要对称开设,只管即便开设在制件厚壁部位,应增加冷料井容积。
3.塑料方面:
结晶性的塑料比非结晶性塑料紧缩历害,加工时要适当增加料量,或在塑估中加成换剂,以加快结晶,减少紧缩凹陷。
4.加工方面:
(1)料筒温度过高,容积变革大,特殊是前炉温度,对流动性差的塑料应适当提高温度、担保畅顺。
(2)注射压力、速率、背压过低、注射韶光过短,使料量或密度不敷而紧缩压力、速率、背压过大、韶光过长造成飞边而涌现紧缩。
(3)加料量即缓冲垫过大时花费注射压力,过小时,料量不敷。
(4)对付不哀求精度的制件,在注射保压完毕,外层基本冷凝硬化而夹心部份尚优柔又能顶出的制件,及早出模,让其在空气或热水中缓慢冷却,可以使紧缩凹陷平缓而不那幺显眼又不影相应用。
(5)“凹痕”是由于浇口封口后或者缺料注射引起的局部内紧缩造成的。注塑制品表面产生的凹陷或者微陷是注塑成型过程中的一个老问题。凹痕一样平常是由于塑料制品壁厚增加引起制品紧缩率局部增加而产生的,它可能涌如今外部尖角附近或者壁厚突变处,如突出、加强筋或者支座的背后,有时也会涌如今一些不常见的部位。产生凹痕的根本缘故原由是材料的热胀冷缩,由于热塑性塑料的热膨胀系数相称高。膨胀和紧缩的程度取决于许多成分,个中塑料的性能,最大、最小温度范围以及模腔保压压力是最主要的成分。还有注塑件的尺寸和形状,以及冷却速率和均匀性等也是影响成分。塑料材料模塑过程中膨胀和紧缩量的大小与所加工塑料的热膨胀系数有关,模塑过程的热膨胀系数称为“模塑紧缩”。随着模塑件冷却紧缩,模塑件与模腔冷却表面失落去紧密打仗,这时冷却效率低落,模塑件连续冷却后,模塑件不断紧缩,紧缩量取决于各种成分的综合浸染。模塑件上的尖角冷却最快,比其它部件更早硬化,靠近模塑件中央处的厚的部分离型腔冷却面最远,成为模塑件上末了开释热量的部分,边角处的材料固化后,随着靠近制件中央处的熔体冷却,模塑件仍会连续紧缩,尖角之间的平面只能得到单侧冷却,其强度没有尖角处材料的强度高。制件中央处塑料材料的冷却紧缩,将部分冷却的与冷却程度较大的尖角间相对较弱的表面向内拉。这样,在注塑件表面上产生了凹痕。凹痕的存在解释此处的模塑紧缩率高于其周边部位的紧缩。如果模塑件在一处的紧缩高于另一处,那幺模塑件产生翘曲的缘故原由。模内残余应力会降落模塑件的冲击强度和耐温性能。有些情形下,调度工艺条件可以避免凹痕的产生。例如,在模塑件的保压过程中,向模腔额外注入塑料材料,以补偿模塑紧缩。大多数情形下,浇口比制件其它部分薄得多,在模塑件仍旧很热而且持续紧缩时,小的浇口已经固化,固化后,保压对型腔内的模塑件就不起浸染。半结晶塑料材料的模塑件紧缩率高,这使得凹痕问题更严重;非结晶性材料的模塑紧缩较低,会最大程度地减小凹痕;添补和坚持增强的材料,其紧缩率更低,产生凹痕的可能性更小。厚的注塑件冷却韶光长,会产生较大的紧缩,因此厚度大是凹痕产生的根本缘故原由,设计时应加以把稳,要只管即便避免厚壁部件,若无法避免厚壁不见,应设计成空心的,厚的部件就平滑过度到公称壁厚,用大的圆弧代替尖角,可以肃清或者最大限度地减轻尖角附近产生的凹痕
(二十三)开裂
开裂,包括制件表面丝状裂纹、微裂、顶白、开裂及因制件粘模、流道粘模而造成或创伤危急,按开裂韶光分脱模开裂和运用开裂。裂纹是指开模或顶出时成型品分裂的一种征象。
成型品偏脆或脱模不良时有时就会产生裂纹。
基本缘故原由与脱模不良相同,如制品粘在模芯上、加强筋、凸台的添补过度等。此外顶出针的速率也会也会影响到裂纹的产生。速率越高,则越随意马虎发生分裂可列举多种缘故原由,不过首先还是树脂老化。尤其要把稳PBT树脂在机筒内的加水分解。其次是结晶化程度不敷。模具温度偏低时必须特殊把稳。
剖析如下:
1.加工方面:
(1)加工压力过大、速度过快、充料愈多、注射、保压韶光过长,都会造成内应力过大而开裂。
(2)调节开模速率与压力防止快速强拉制件造成脱模开裂。
(3)适当调高模具温度,使制件易于脱模,适当调低料温防止分解。
(4)预防由于熔接痕,塑料降解造成机器强度变低而涌现开裂。
(5)适当利用脱模剂,把稳常常肃清模面附着的气雾等物质。
(6)制件残余应力,可通过在成型后立即进行退火热处理来肃清内应力而减少裂纹的天生。
遵守各材料的推举成形温度,并缩短勾留韶光以减少树脂的分解老化。如果是PBT等聚酯类树脂,强化干燥条件也是抑制加水分解的一种有效方法。还可以通过提高模具温度和延长冷却韶光来提高产品的结晶化程度。
此外采取下列方法也有效果:
•减慢开模速率和顶出速率以减轻成型品所承受的负荷以减少裂纹。
•给成型品的转角处增设R(圆角)以防分裂。
2.模具方面:
(1)顶出要平衡,如顶杆数量、截面积要足够,脱模斜度要足够,型腔面要有足够光滑,这样才防止由于外力导致顶出残余应力集中而开裂。
(2)制件构造不能太薄,过渡部份应只管即便采取圆弧过渡,避免尖角、倒角造成应力集中。
(3)只管即便少用金属嵌件,以防止嵌件与制件紧缩率不同造成内应力加大。
(4)对深底制件应设置适当的脱模进气孔道,防止形成真空负压。
(5)主流道足够大使浇口料未来得及固化时脱模,这样易于脱模。
(6)主流道衬套与喷嘴接合应该防止冷硬料的拖沓而使制件粘在定模上。
3.材料方面:
(1)再生料含量太高,造成制件强度过低。
(2)湿度过大,造成一些塑料与水汽发生化学反应,降落强度而涌现顶出开裂。
(3)材料本身不适宜正在加工的环境或质量佳,受到污染都会造成开裂。
4.机台方面:注塑机塑化容量要适当,过小塑化不充分未能完备稠浊而变脆,过大时会降解。
(二十四)制件尺寸不稳定
制件尺寸变革,实质上是塑料不同紧缩程度所造成的。凡是料温、模具、压力、生产周期变革不定的操作,都将导致制件尺寸的变革,尤其是结晶度较大的PP、PE、尼龙等是如此。
剖析如下:
1.机台方面:
(1)塑化容量不敷应选用塑化容量大的机台。
(2)供料不稳定,应检讨机台的电压是否颠簸,注射系统的组件是否磨损或液压阀方面是否有问题。(3)螺杆转速不稳定,应检讨马达是否有故障,螺杆与料筒是否磨损,液压阀是否卡住,电压是否稳定。(4)温度失落控,比例阀、总压力阀事情不正常,背压不稳定。
2.模具方面:
(1)要有足够的模具强度和刚性,型腔材料要采取耐磨材料。
(2)尺寸精度哀求很高时,只管即便不采取一模多腔形式。
(3)顶出系统、浇注系统、冷却系统要设置合理,担保生产条件的稳定。
3.塑料方面:
(1)新料与再生料的稠浊要同等。
(2)干燥条件要同等,颗粒要均匀。
(3)选料时充分考虑紧缩率对尺寸精度的影响。
4.加工方面:
(1)塑料加工温度过低,应提高温度,由于温度越高,尺寸收 缩越小。
(2)对结晶型塑料,模具温度要低些。
(3)成型周期要保持稳定,不能过大的颠簸。
(4)加料量即射胶量要稳定。
(二十五)肿胀与鼓泡
有些塑料制件在成型脱模后,很快在金属嵌件的背面或在特殊厚的部位涌现肿胀或鼓泡。这是由于未完备冷却硬化的塑料在内压罚的浸染下开释气体膨胀造成。
办理方法:
1.有效的冷却。降落模温,延长开模韶光,降落料的干燥与加 工温度。
2.降落充模速率,减少成形周期,减少流动阻力。
3.提高保压压力和韶光。
4.改进制件壁面太厚或厚薄变革大的 状况。
(二十六)气泡(真空泡)
气泡的气体十分稀薄属于真空泡。一样平常说来,如果在开模瞬间已创造存在气泡是属于气体滋扰问题。真空泡的形成是由于充注进塑料不敷或压力较低。在模具的急剧冷却浸染下,与型腔接角的燃料牵拉,造成体积丢失的结果。
气泡是指成型品表面鼓起的一种征象。
以下二种情形随意马虎涌现气泡,即注射成型后从模具取出时,制品表面开始逐渐鼓起和成型品表面因受热膨胀而鼓起时。不论哪种情形,当成型品表面因高温而变软时,内部的气体都会因受热膨胀而将成型品表面顶起,从而形成气泡。如果计量时卷入了大量空气,则随意马虎产生气泡。详细来说也便是螺杆转速快、背压低并且抽塑量多的时候随意马虎产生气泡。此外,在模腔添补过程中,有些流动样式有时也会卷入空气,从而产生气泡。如果表层与芯层之间的结合很弱,或者存在眇小的空洞或裂纹,则很随意马虎以此为出发点产生气泡。详细来说,在成型薄壁制品因强行添补导致应变残留在制品中,或冷料或喷射纹的混入等。特殊是在液晶高分子中,由于层间强度不高(这是树脂的固有性子),因此很随意马虎产生气泡。
从成形条件来看,注射速率快时,气泡将涌现恶化的方向。此外,在浇口偏小的情形下,由于会产生喷射纹,同时很大的剪切力会导致应变残留,因此气泡也会涌现恶化的方向。
树脂中产生的大量气体也随意马虎产生气泡。当机筒温度过高,滞留韶光偏永劫,所产生的气体会增多,从而也随意马虎产生气泡。此外,干燥不敷,材料中所含的水分过多时,也会产生气泡。
办理方法:
(1)提高注射能量:压力、速率、韶光和料量,并提高背压, 使充模丰满。
(2)增加料温流动顺畅。降落料温减少紧缩,适当提高模温, 特殊是形成真空泡部位的局部模温。
(3)将浇口设置在制件厚的部份,改进喷嘴、流道和浇口的流 动状况,减少压务的花费。
(4)改进模具排气状况。
要减少计量中的空气卷入,应变动下列条件:
•降落螺杆转速
•提高背压
•抽塑量设定不要过多
如果在模腔添补期间涌现空气卷入征象,则须要调度形状、浇口位置以及射出速率。这一点应根据成形品的情形来详细应对。通过添补不敷(short shot),把握住流动样式,然后在此根本上确立相应的对策。改变保压等对改进气泡没什幺效果,倒不如减少添补时的剪切力以使材料能顺利地充满模腔对肃清气泡会更有效。详细来说,可变动下列成型条件:
•提高模具温度
•减慢注射速率
•增大浇口
•增加厚度(仅对付过薄的部分)
•避免产生喷射纹
(二十七)熔接缝
表不雅观在充模办法里,熔接缝是指各流体前审察遇时的一条线。特殊是模具有高抛光表面的地方,制品上的熔接缝很象一条刮痕或一条槽,尤其是在颜色深或透明的制品上更明显。熔接缝的位置总是在料流方向上。
物理缘故原由
熔接缝形成的地方为熔料的细流分叉并又连接在一起的地方,最范例的是型芯周围的熔流或利用多浇口的制品。在细流再次相遇的地方,表面会形成熔接缝和料流线。熔料周围的型芯越大或浇口间的流道越长,形成的熔接缝就越明显。眇小的熔接缝不会影响制品的强度。
然而,流程很长或温度和压力不敷的地方,充模不满会造成明显的凹槽。缘故原由紧张是流体前端未均匀熔合产生弱光点。聚合物内加入颜料的地方可能会产生斑点,这是由于在取向上有明显的差异。浇口的数量和位置决定了熔接缝的数量和位置。流体前锋相遇时的角度越小,熔接缝越明显。
大多数情形下,工艺调试不可能完备避免熔接缝或料流线。所能做到的是降落其亮度,或将它们移到不显眼或完备看不见的地方
与加工参数有关的缘故原由与改良方法见下表:
1、注射速率太低增加注射速率
2、熔料温度太低提高料筒温度
3、模具表面温度太低增加模具温度
4、保压太低增加保压,尽早进行保压切换
5、浇口位置不合理重新定位浇口并将其移到不可见的地方
6、料流道处无排气孔排气孔尺寸应符合材料的特性
(二十八)塑料制品发脆的缘故原由
发脆
制品发脆很大一部分是由于内应力造成的。造成制品发脆的缘故原由很多,紧张有:
一设备方面
(1)机筒内有角或障碍物,随意马虎促进熔料降解。
(2)机器塑化容量太小,塑料在机筒内塑化不充分;机器塑化容量太大,塑料在机筒内受热和受剪切浸染的韶光过长,塑料随意马虎老化,使制品变脆。
(3)顶出装置倾斜或不平衡,顶干截面积小或分布不当。
二模具方面
(1)浇口太小,应考虑调度浇口尺寸或增设赞助浇口。
(2)分流道太小或配置不当,应只管即便安排得平衡合理或增加分流道尺寸。
(3)模具构造不良造成注塑周期反常。
三工艺方面
(1)机筒、喷嘴温度太低,调高它。如果物料随意马虎降解,则应提高机筒、喷嘴的温度。
(2)降落螺杆预塑背压压力和转速,使料稍为疏松,并减少塑料因剪切过热而造成的降解。
(3)模温太高,脱模困难;模温太低,塑料过早冷却,熔接缝领悟不良,随意马虎开裂,特殊是高熔点塑料如聚碳酸酯等更是如此。
(4)型腔型芯要有适当的脱模斜度。型芯难脱模时,要提高型腔温度,缩短冷却韶光;型腔难脱时,要降落型腔温度,延长冷却韶光。
(5)只管即便少用金属嵌件,象聚苯乙烯这类脆性的冷热比容大的塑料,更不能加入嵌件注塑。
四质料方面
(1)质料混有其它杂质或掺杂了不适当的或过量的溶剂或其它添加剂时。
(2)有些塑料如ABS等,在受潮状况下加热会与水汽发生催化裂化反应,使制件发生大的应变。
(3)塑料再生次数太多或再生料含量太高,或在机筒内加热韶光太长,都会匆匆使制件脆裂。
(4)塑料本身质量不佳,例如分子量分布大,含有刚性分子链等不屈均构造的身分霸占量过大;或受其它塑料掺杂污染、不良添加剂污染、灰尘杂质污染等也是造成发脆的缘故原由。
五制品设计方面
(1)制品带有随意马虎涌现应力开裂的尖角、缺口或厚度相差很大的部位。
(2)制品设计太薄或镂空太多。
(二十九) 白边
白边是改性聚乙烯和有机玻璃特有的注射毛病,大多涌如今靠近分型面的制件边缘上。白边是由无数与料流方向垂直的拉伸取向分子和它们之间的微细间隔组成的凑集体。在白边方向上尚存在高分子连接相,因而白边还不是裂痕,在适当的加热下,有可能使拉伸取向分子回答自然卷曲状态而使白边消退。
办理方法:
(1)生产过程把稳保持模板分型面的紧密吻合,特殊是型腔周围区域,一定要处于真正充分的锁模力下,避免纵向和横向胀模。
(2)降落注射压力、韶光和料量,减少分子的取向。
(3)在模面白边位置涂油质脱模剂,一方面使这个位置不易传热,高温韶光坚持多一些,另一方面使可能涌现白边受到抑制。
(4)改进模具设计。如采取弹性变形量较小的材料制作模具,加强型腔侧壁和底板的机器承载力,使之足以承受注射时的高压冲击和事情过程温度的急剧升高,对白边易发区给予较高的温度补偿,改变料流方向,使型腔内的流动分布合理。
(5)考虑换料。
白霜
有些聚苯乙烯类制件,在脱模时,会在靠近分型面的局部表面创造附着一层薄薄的白霜样物质,大多经抛光后能撤除。这些白霜样物质同样会附在型腔表面,这是由于塑料原估中的易挥发物或可溶性低分子量的添加剂受热后形成气态,从塑料熔体释出,进入型腔后被挤迫到靠近有排气浸染的分型面附近,沉淀或结晶出来。这些白霜状的粉末和晶粒粘附在模面上,不单会刮伤下一个脱模制件,次数多了还将影响模面的光洁度。不溶性填料和着色剂大多与白霜的涌现无关。白霜的办理方法:加强质料的干燥,降落成型温度,加强模具排气,减少再生料的掺加比例等,在涌现白霜时,特殊要把稳常常清洁模面。
(三十)制件不满(充填不敷)
缘故原由紧张是缺料和注射压力与速率欠妥(包括阻力造成压力过于消耗)。充填不敷是指无法完备添补成型品。
正常品会得到与模具同等的产品,而充填不敷品则无法得到所希望的形状。
充填不敷是在树脂流动性不敷或树脂计量值偏少时产生的。
1. 机台方面:
机台的塑化量或加热率不定,应选用塑化量与加热功率大的机台;
螺杆与料筒或过胶头等的磨损造成回料而涌现实际充模量不中;热电偶或发热圈等加热系统故障造成料筒的实际温度过低;注射油缸的密封组件磨损造成漏油或回流,而不能达到所需的注射压力;射嘴内孔过小或射嘴中央度调节不当造成阻力过大而使压力花费。
2. 模具方面
(1).模具局部或整体的温度过低造成入料困难,应适当提高模
(2).模具的型腔的分布不平衡。制件壁厚过薄造成压力花费过磊而且充模不力。应增加全体制件或局部的壁厚或可在添补不敷处的附近,设置赞助流或浇口办理。3).模具的流道过小造成压力损耗;过大时会涌现射胶无力;过于粗糙都会造成制件不满。应适当设置流道的大小,主流道与分流道,浇口之间的过渡或本身的转弯处运用适当的圆弧过渡。 4).模具的排气不良。进入型腔的料受到来不及排走的气体压力的阻挡而造成充填不满。可以充分利用螺杆的缝隙排气或降落锁模力利用分型面排气,必要时要开设排气沟道或气孔。产品形状和模具布局也是产生充填不敷的缘故原由。浇口尺寸偏小、分流道偏细时流动性会降落,因此也很随意马虎导致充填不敷。此外,如果产品的壁厚偏薄,当然也很随意马虎发生充填不敷。
加工,调度方面:注塑压力太小,速率太慢,韶光太短,温度太低,熔料位置偏小。
如果只是由于流动性不敷而导致充填不敷的话,则估计有以下几种条件:
(1)树脂温度偏低
(2)模具温度偏低
(3)材料流动性不敷
(4)注射速率偏低
(5)注射压力偏低
如果计量值少于产品所需的量,则一定导致充填不敷。有时不仅是因计量值偏少,而且还会因计量不良所产生的差错而导致充填不敷。检讨是否充分进行过预干燥。为每种树脂所推举的干燥条件都标注在产品袋上。请将实际结果与该值进行比拟。
同时还应检讨流动末端的排气口是否无缺。如果有烧焦的迹象,则很可能排气不良。应设法扩大或添加排气口。
如果因与上述相同的缘故原由而产生大量气体,则在流动末端有时也会涌现充填不敷。必须预前辈行适度干燥以去除水分等。是指注射→保压的切换位置。如果这统统换位置过早(也便是过早地转移到保压阶段),流动性就会整体低落,从而导致充填不敷。检讨是否充分进行过预干燥。为每种树脂所推举的干燥条件都标注在产品袋上。请将实际结果与该值进行比拟。
同时还应检讨流动末端的排气口是否无缺。如果有烧焦的迹象,则很可能排气不良。应设法扩大或添加排气口。
(三十一)披锋airtrap(飞边、flash)溢料
披锋又称飞边、溢边、披锋、溢料等,多数发生在模具分合位置上,如:模具的分合面、滑块的滑配部位、镶件的缝隙、顶杆的孔隙等处。溢料不及时办理将会进一步扩大化,从而压印模具形成局部陷塌,造成永久性危害。镶件缝隙和顶杆孔隙的溢料还会使制品卡在模上,影响脱模。虽然制作模具时精度很高(μm级),而且成型时采取高压合模,但由于树脂的添补压力也很高,以是实际上留有很小的缝隙。飞边便是因树脂进入这种缝隙而形成的。在PL面、套管、滑芯界面和排气口等处都会涌现飞边。
飞边便是树脂挤入模具PL面(模具的分型面),并使制品带上了多余的薄膜这样一种征象。当PL面不敌树脂压力而分开,或PL面有缝隙时就会涌现这种情形。
一机器设备方面:
(1)机器真正的合模力不敷。选择注塑机时,机器的额定合模力必须高于注射成型制品纵向投影面积在注射时形成的张力,否则将造成胀模,涌现飞边。
(2)合模装置调节不佳,肘杆机构没有伸直,产生或旁边或高下合模不屈衡,模具平行度不能达到的征象造成模具单侧一边被合紧而另一边不密贴的情形,注射时将涌现飞边。
(3)模具本身平行度不佳,或装得不平行,或模板不平行,或拉杆受力分布不均、变形不均,这些都将造成合模失慎密而产生飞边。
(4)止回环磨损严重;弹簧喷嘴弹簧失落效;料筒或螺杆的磨损过大;入料口冷却系统失落效造成“架桥”征象;机筒调定的注料量不敷,缓冲垫过小等都可能造成飞边反复涌现,必须及时维修或改换配件。
二模具方面
(1)模具分型面精度差。活动模板(如中板)变形翘曲;分型面上沾有异物或模框周边有凸出的橇印毛刺;旧模具因起先的飞边挤压而使型腔周边疲倦塌陷。
(2)模具设计不合理。模具型腔的开设位置过偏,会令注射时模具单边发生张力,引起飞边;塑料流动性太好,如聚乙烯、聚丙烯、尼龙等,在熔融态下黏度很低,随意马虎进入活动的或固定的缝隙,哀求模具的制造精度较高;在不影响制品完全性的条件下应只管即便安置在质量对称中央上,在制品厚实的部位入料,可以防止一边缺料一边带飞边的情形;当制品中心或其附近有成型孔时,习气上在孔上开设侧浇口,在较大的注射压力下,如果合模力不敷模的这部分支承浸染力不足发生轻微翘曲时造成飞边,如模具侧面带有活动构件时,其侧面的投影面积也受成型压力浸染,如果支承力不足也会造成飞边;滑动型芯合营精度不良或固定型芯与型腔安装位置偏移而产生飞边;型腔排气不良,在模的分型面上没有开排气沟或排气沟太浅或过深过大或受异物壅塞都将造成飞边;对多型腔模具应把稳各分流道合浇口的合理设计,否则将造成充模受力不均而产生飞边。纵然在大略的2块式模具中,模具有时也会因成型品顶出不当而受损,并在损伤处涌现飞边。利用滑芯时,必须特殊把稳吻合以及滑动面的缝隙。
其余,模具是钢制的,合模压属于高压,而树脂压也是与其相称的高压,以是在险些所有的注射成型中,模具一样平常都会发生变形。特殊是在大型成型品的情形下尤为显著。此时,有无支柱对飞边也有影响(如果没有支柱,变形→缝隙就会增大,飞边也会增多)。
三工艺方面
(1)注射压力过高或注射速度过快。由于高压高速,对模具的伸开力增大导致溢料。要根据制品厚薄来调节注射速率和注射韶光,薄制品要用高速迅速充模,充满后不再进注;厚制品要用低速充模,并让表皮在达到终压前大体固定下来。
(2)加料量过大造成飞边。值得把稳的是不要为了防止凹陷而注入过多的熔料,这样凹陷未必能“填平”,而飞边却会涌现。这种情形运用延长注射韶光或保压韶光来办理。
(3)机筒、喷嘴温度太高或模具温度太高都会使塑料黏度低落,流动性增大,在流畅进模的情形下造成飞边。
四质料方面
(1)塑料黏度太高或太低都可能涌现飞边。黏度低的塑料如尼龙、聚乙烯、聚丙烯等,则应提高合模力;吸水性强的塑料或对水敏感的塑料在高温下会大幅度的降落流动黏度,增加飞边的可能性,对这些塑料必须彻底干燥;掺入再生料太多的塑料黏度也会低落,必要时要补充滞留身分。塑料黏度太高,则流动阻力增大,产生大的背压使模腔压力提高,造成合模力不敷而产生飞边。树脂压力过高时,模具分开并产生飞边。相反,模具压力偏低时,同样也随意马虎产生飞边。树脂压力增高的紧张缘故原由如下:PSS树脂在低剪切区的流动性很强,因此该树脂就其本身的性子而言就具有随意马虎产生飞边的缺陷。因此,与利用其它材料时比较,利用PPS树脂时必须更加把稳防止涌现飞边。此时对模具精度等级的哀求也比利用其它材料时更加严格。
(1)注速率偏快
(2)注射压力偏高
(3)保压力偏高
(4)V-P切换偏慢
一样平常来说,当希望得到良好的外不雅观时,有时会将保压设定的过高,特殊是为了防止涌现凹痕而采取高于标准的设定。这样一来有时就会产生飞边。流动性越好,树脂就越随意马虎进入缝隙,因此飞边也就越大。一样平常来说,树脂温度和模具温度越高,飞边也就越大;反之,温度越低,飞边也就越小。
(2)塑料质料粒度大小不均时会使加料量变革不定,制件或不满,或飞边。
故障缘故原由 处理方法
塑料温度太高 降落塑料温度,降落模具温度
射胶速率太高 降落射胶速率
射胶压力太高 降落射胶压力
填料太饱 降落射胶韶光,速率及剂量
合模线或吻合面不良 检修模具
锁模压力不足 增加锁模压力或改换模压力较大的注塑机
1 滑块与定位块如果磨损,则随意马虎涌现毛边。
2 模具表面附着异物时,也会涌现毛边。
3 锁模力不敷,射出时模具被打开,涌现毛边。
4 质料温度以及模具温度过高,则粘度低落,以是在模具仅有间隙上也随意马虎产生毛边。
5 料量供给过多,质料多余射动身生毛边。
毛边缘故原由
成
型
机
计量多(过分充填)
射出压力高
射出速率快
质料温度高
锁模力低
射出韶光长
保压压力高
保压压力转换位置慢
计量不准确,有偏差(背压、螺杆转速)
机台固、定板可动板平行不良
模
具
合模面打仗不良
模具打仗面上附有异物
模穴内有碰伤
模具温度高
模具刚性不良(强度不敷)
滑动部位间隙合营不良
模具构造设计
原
料
质料的流动性太好
注射成型——注射成型又称注射模塑或注塑,此种成型方法是将塑料(一样平常为粒料)在注射成型
机料筒内加热熔化,当呈流动状态时,在柱塞或螺杆加压下熔融塑料被压缩并向前移动,进而通过料
筒前真个喷嘴以很快速率注入温度较低的闭合模具内,经由一定韶光冷却定型后,开启模具即得制品。
注射成型是根据金属压铸事理发展起来的。由于注射成型能一次成型制得形状繁芜、尺寸精确,
或带有金属嵌件得制品,因此得到广泛的运用,目前占成型加工总量的20%以上。
注射成型过程常日由塑化、充模(即注射)、保压、冷却和脱模等五个阶段组成。
一样平常的注射成型制品都有浇口、流道等废边料,需加以修整撤除。这不仅耗费工时,也摧残浪费蹂躏质料。
近年来发展的无浇口注射成型不仅战胜了上述弊端,还有利于提高生产效率
(三十二)塑件光泽不良(玻纤析出)
何谓光泽不好?
光泽不好是指成型品未粘着在模具上,即复制不良。
光泽不好的天生缘故原由
(2-1)由喷射纹或冷料引起
成形品表面涌现喷射纹或冷料时,因其与周围不同,因此看起来像雾一样模糊不清。多涌如今浇口附近及高低不平之处。
(2-2)因气体缘故原由
这是由于气体被封堵在模具与树脂之间并妨碍两者间的粘合而发生的光泽不好。保压力偏低或排气不畅时更随意马虎涌现。
(2-3)因压力不敷
因压力偏低,因而对树脂的模具面的挤压力偏弱而引起的光泽不好。在含玻纤等填料的材料中,由于填料随意马虎浮出表面(树脂随意马虎沉入内侧),因此光泽不好变得更为明显。
例如,当注射速率偏低时,压力因树脂固化而无法通报到末端,从而随意马虎在成形品末端产生光泽不好。同时,当模具温度偏低,整体固化偏快时,全体成型品上也随意马虎涌现光泽不好。
(3)光泽不好的对策
首先考试测验提高保压设定值和保压韶光设定值。此时应看到情形在改进。如果没有,则可认为是由于其它缘故原由而使该部分的实际压力上升不敷。此时应同时利用下列对策:
提高模具温度
提高机筒温度(特殊是喷嘴)
增大浇口尺寸
提高注射速率
利用流动性好的材料等级
一、注塑模具方面
1.若模具型腔加工不良,如有伤痕、微孔、磨损、粗糙等不敷,势必会反应到塑件上,使塑件光泽不良,对此,要精心加工模具,使型腔表面有较小的粗糙度,必要时可抛光镀铬。
2.若型腔表面有油污、水渍,或脱模剂使太多,会使塑件表面发暗、没有光泽,对此,要及时打消油污和水渍,并限量利用脱模剂。
3.若塑件脱模斜度太小,脱模困难,或脱模时受力过大,使塑件表面光泽佳,对此,要加大脱模斜度。
4.若模具排气不良,过多气体勾留在模型内,也导致光泽不良,对此,要检讨和改动模具排气系统。
5.若浇口或流道截面积过小或溘然变革,熔体在个中流动时受剪力浸染太大,呈湍流动态流动,导致光泽不良,对此,应适当加大浇口和流道截面积。
必须检讨气体是否已打消干净。
检讨是否确保了有效排出气体所需的排气口厚度和大小、是否受到模垢的污染等。是否被配置到适当位置也很主要。如果可能,建议采取充填不敷(short shot)方法以理解实际的树脂流动状况。
二、注塑工艺方面
1.若注射速度过偏小,塑件表面不密实,显现光泽不良,对此,可适当提高注射速率。
2.对付厚壁塑件,如冷却不充分,其表面会发毛,光泽偏暗,对此,应改进冷却系统。
3.若保压压力不敷,保压韶光偏短,使塑件密度不足而光泽不良,对此,应增大保压压力和保压韶光。
5.若熔体温度过低,使得流动性较差,易导致光泽不良,对此,应适当提高熔体温度。
6.对付结晶树脂,如PE、PP、POM等制作的塑件,如冷却不屈均会导致光泽不良,对此,应改进冷却系统,使之均匀冷却。
7.若注射速度过大,而浇口截面积又过小,则浇品附近会发暗而光泽不良,对此,可适当降落注射速率和增大浇口截面积。
三、原材料方面
1.原材料粒度差异较大,使得难以均匀塑化,而光泽不良,对此应将原材料进行筛分处理
2.原估中再生料或水口料加入太多,影响熔体的均匀塑化而光泽不良,对此,应减少再生料或水口料加入量。
3.有些原材料在调温时会分解变色导致光泽不良,对此,应选用耐温性较好的原材料。
4.原材料中水分或易挥发物含量过高,受热时挥发成气体,在型腔和熔体中凝缩,导致塑件光泽不良,对此,应对原材料进行预干燥处理。
5.有些添加剂的分散性太差而使塑件光泽不良,对此,应改用流念头能较好的添加剂。
6.原材料中混有异物,杂料或不相溶的物料,它们不能与其质料均匀混熔在一起而导致光泽不良,对此,应事先严格打消这些杂料。
7.若润滑剂用量过少,熔体的流动性较差,塑件表面不致密,使得光泽不良,对此,应适当增加润滑剂的用量。
(三十三)变色和焦化或黑点
何谓变色(外不雅观)?
变色是指成型品的颜色变得与正常颜色不同。由于塑料是化学物质,因此当在熔点以上连续加热时,它便会逐渐分解和变质。变色便是与此过程相伴而生的。
紧张缘故原由是塑料或添加的紫外线接管剂、防静电剂等在料筒内过热分解,或在料筒内勾留韶光过长而分解、焦化,再随同熔料注入型腔形成。
(2)变色的天生缘故原由
机筒内部的热变色
机筒内部已融化的树脂常常处于高温状态,设定温度越高,滞留韶光越长,变色也就越厉害。其余,计量时所施加的剪切力也是变色的缘故原由之一。螺杆转速越高,剪切力也就越大,变色也就越随意马虎。要抑制机筒内的树脂变色,应降落树脂温度(包括喷嘴)并缩短滞留韶光。
1.机台方面:
(1)由于加热掌握系统失落控,导致料筒过热造身分化变黑。
(2)由于螺杆或料筒的毛病使熔料卡入而屯积,经受永劫光固定加热造身分化。应检讨过胶头套件是否磨损或里面是否有金属异物。
(3)某些塑料如ABS在料筒内受到高热而交联焦化,在险些坚持原来颗粒形状环境下,难以熔融,被螺杆压破碎后夹带进入制件。
2.模具方面:
注射速度过快时,模具内部的剪切力也会增大。浇口或喷嘴偏小时,剪切力有时也会增强并引起变色。如果喷嘴、浇口等模具内的特定部分发生变色,则应降落注射速率。建议此时采取多级注射等。
(1)模具排气不衣,易烧焦,或浇注系统的尺寸过小,剪切过于历害造成焦化。
(2)模内有不适当的油类润滑剂、脱模剂。
3.塑料方面:
塑料挥发物过多,湿度过大,杂质过多,再生料过多,受污染。
4.加工方面:
(1)压力过大,速度过高,背压过大,如果计量时发生变色转速过快都会使料温分解。
(三十四)烧焦纹(Charredstreaks)
表不雅观制品表面表现出银色和淡棕色的非常暗的条纹。气体烧焦是指在成型时成型品表面的烧焦征象。当树脂添补模腔时,原有的空气会从排气口排出。此时,树脂所产生的气体也会从排气口排出。但是,如果模具的排气口被堵塞,或流动末端本来就没有排气口,气体便无法排出,受到压缩后形成高温,从而导致树脂被烧焦。
随着树脂的添补,模腔内的空气和树脂中所含的气体会从排气口排出。但是,如果射出速率太快,气体就会来不及从排气口排出,并会因受到隔热压缩而形成高温,进而导致气体烧焦。VP切换偏慢时,也会因同样的缘故原由而随意马虎产生气体烧焦。
与上述情形类似,当排气口的排气能力偏低时,也会发生气体烧焦。缘故原由有两种:一种是排气口的厚度本来就偏薄,另一种是在利用期间排气口被模垢堵塞。同样的道理,当树脂中蕴含的气体量偏多时,气体烧焦也会加重。当模具温度或树脂温度偏高时(虽说是次要缘故原由),气体烧焦也有加重的趋势。
物理缘故原由
烧焦暗纹是由于熔料过度热降解而造成的。淡棕色的黯纹是由于熔料发生氧化或分解。银纹的造成一样平常是由于螺杆、止逆环、喷嘴、料头、制品内窄的横截面或锐边区域产生摩擦。
一样平常来说,在机器歇工而料筒仍连续加热的韶光内塑料会发生严重降解或分解征象。
如果仅在料头附近创造条纹,缘故原由就不止是热流道温度掌握优化不敷,还同机器的喷嘴有关。
熔料的温度哪怕是轻微有点高,熔料在料筒内的残留韶光相对较长,也会导致制品的力学性能低落。在由于分子热运动而产生的降解连锁反应的浸染下,熔料的流动性会增加,以至让模件不可避免地发生溢模的征象。对繁芜模具尤其要小心。
与加工参数有关的缘故原由与改良方法见下表:
1、熔料温度太高低降料筒温度
2、热流道温度太高检讨热流道温度,降落热流道温度
3、熔料在料筒内残留韶光太长采取小直径料筒
4、注射速率太高减小注射速率:采取多级注射:快-慢
气体烧焦是因气体被急剧压缩并形成高温而引起的。因此减慢注射速率可降落气体烧焦。当成型品的形状受到限定时,请调度VP切换位置或利用多段注射。如果无论如何也办理不了问题,则应通过强化排气口等方法来改进排气状况。
(三十五)空穴(空洞)
1. 注塑件毛病的特色
是指成型品内部产生空洞的一种征象。
可以随意马虎地在透明注塑件的“空气阱”内见到但也可涌如今不透明的塑估中。
这与厚度有关,而且常因塑料紧缩离开注塑件中央而引起。空洞的缘故原由大致分为两种:一种是大量气体的混入,另一种则是厚壁处的的树脂紧缩。前者称为“气体空洞”,后者称为“真空空洞”,以示差异气体空洞有两种类型:一种是由机筒内部产生的气体引起的,另一种是在模腔添补中封入了气体所致。
前一种空洞的气体身分有3种:水分、树脂的分解气体和空气。预干燥不敷时随意马虎产生水分;机筒温度高且滞留韶光永劫随意马虎产生树脂的分解气体;计量期间螺杆转速过快且背压不敷时随意马虎产生空气。
后一种空洞取决于树脂的流动样式,因此缘故原由在于浇口设计。就成型条件而言,如果注射速率很快、没有排气口、或排气不充分,则随意马虎产生空洞。常日,注射成型中有一道保压工序,冷却固化→紧缩的树脂量将通过保压来得到补充。不过,如果因某种缘故原由使有效保压偏低=树脂难以的到充补,当模温偏高时就随意马虎形成凹痕,而在模温偏低时随意马虎形成空洞。导致保压变小的紧张缘故原由如下:
2.可能涌现问题的缘故原由
(1).模具未充分添补。
(2).止流阀的不正常运行。
(3).塑料未彻底干燥。
(4).预塑或注射速度过快。
(5).某些分外材料运用分外的设备生产
(6)保压设定值偏低
(7)保压韶光偏短
(8)浇口尺寸偏小
(9)分流道偏细
此外,鉴于浇口位置的主要性,必须尽可能将其设置在厚壁处。
3.补救方法
无论是气体形成的空洞还是紧缩形成的空洞,共同之处都在于通过妥善地补充树脂使问题得到改进。例如,通过提高保压(延长保压韶光)可使情形发生显著变革。就提高保压的方法而言,与大略地调高保压的设定值比较,采取多段保压效果会更好。
但是,在实际成型中,纵然提高保压的设定值,施加在空洞涌现部位的压力也未必能变得足够大。因此建议同时采取下列方法:
•增大浇口尺寸
•增大主流道和分流道的口径
•浇口应尽可能设在空洞产生部位(较厚部分)的附近
(1).增加射料量。
(2).增加注塑压力。
(3).增加螺杆向前韶光。
(4).降落熔融温度。
(5).降落或增加注塑速率。(例如对非结晶体类的塑料要增
加45%速率)。
(6).检讨止逆阀是否裂开或无法运作。
(7).应根据塑料的特性改进干燥条件,让塑料彻底干燥。
(8).适当降落螺杆转速和增大背压,或降落注射速率。
如果是真空空洞,则提高模具温度可以减少空洞。不过,这种方法很可能会诱发凹痕,而且对有些产品来说,没有什幺好的办理方法。如果是气体空洞,则可通过抑制气体的产生来减轻空洞。详细方法如下:
•强化预干燥条件
•降落机筒设定温度
•缩短成型周期
•降落螺杆转速
•提高背压
对付模腔添补中因封入气体而产生的空洞,可通过降落注射速率、或强化排气口以改进排气状况来减少空洞的产生。
由于厚壁处涌现的真空空洞起因于树脂紧缩,因此可能的话,该当考虑变动制品形状以减少厚度。可能的话,最好在设计阶段就事先采纳“掏空”等改变制品形状的方法。粘度型的材料一样平常不随意马虎涌现空洞,因此考试测验利用这种材料也不失落为一种方法。
(三十六) 须状斑纹(1) 何谓须状斑纹
(2)须状斑纹的天生缘故原由
流动样式的变革
(3)须状斑纹的对策
改进浇口处的流动状况
(1) 何谓须状斑纹(外不雅观)
须状斑纹是指在Duracon中常见的、浇口附近的小流痕。
斑纹本身很薄,难以拍摄,如右图所示。
(2) 须状斑纹的天生缘故原由
(2-1) 流动样式的变革
从浇口出来的树脂常日是按左边的样式来添补的,而当按右边的样式流动时便会产生“须状斑纹”。就成型条件而言,不才列情形下随意马虎产生须状斑纹:
(1)模具温度偏低
(2)注射速率偏快
(3)浇口尺寸偏小
(4)材料流动性偏低
(3)须状斑纹的对策
(3-1) 改进浇口处的流动状况
详细来说,可采纳下列对策:
(1)提高模具温度
(2)降落注射速率(通过浇口时)
(3)扩大浇口
(4)改用流动性好的等级
要降落通过浇口时的速率,请最好采取多级注射。
另请参阅下述推举成型条件以免形成极度成型条件:
(三十七) 模垢(MD)对策
模垢(MD)一旦形成便很难去除
因此必须在稳定附着前就进行掩护
下面给出的是延长掩护周期的一些对策
(1) 强化预干燥
最好达到100~120℃、3小时的基本标准。但如果干燥温度偏高,则会使Duracon DS-01M、EB-7以及EB-10趋于恶化。(最好达到60℃×18小时的条件)其机制现在尚不清楚。应予以把稳。
(2) 降落机筒温度
应尽可能降落,下限常日为180℃。
(3) 减少树脂的滞留韶光
为了尽可能防止材料的热分解,建议利用较小的成型机并使机筒温度带有梯度。
(4) 提高模具温度
注射树脂时,气体状的MD紧张身分也会被同时注射到模具内。这种身分打仗到模具并连忙冷却后便会凝固并附着在模具上,从而形成MD。由此可见,提高模具温度将有助于防止连忙冷却并增加附矀的难度
(5) 只管即便降落注射速率
为了防止树脂在浇口等流道较窄处因剪切而发热,同时也为了使排气能够顺利进行,注射速率还是慢一点为好。
这一方法会带来令人出人意料的效果。
(6) 尽可能加大浇口直径
对点浇口和隧道浇口特殊有效,与上述⑤一起利用时效果会更加显著。
(7) 定期用清模剂来清理排气口
如上所述,MD积得很厚时将难以清理,但如果只是排气口的清理,则比较随意马虎进行。MD附着的第一步便是从排气口的堵塞开始的。建议在早上开工前和午休后进行清理。
(三十八)浇口残留
(1)何谓浇口残留
(2)浇口残留的天生缘故原由
浇口固化不敷
浇口形状
等级固有的问题
(3)浇口残留的对策
促进浇口固化
变动浇口形状
(1) 何谓浇口残留(外不雅观)
是指浇口残留在成型品表面上的一种征象。
点浇口或隧道浇口在开模时会自动断开,但如果浇口的形状和大小不得当,则不能彻底断开
(2) 浇口残留的天生缘故原由
(2-1) 浇口固化不敷
如果浇口固化不敷,则开模时本该断开的部位以外的部分也变脆,因此浇口也会在该处断开,从而导致浇口的前端部分残留在产品侧。
(2-2) 浇口形状
采取点浇口的情形下,如果浇口前端部分的锥角偏缓,则有时在前端部分无法彻底割断。此外浇口前真个直径大小也会产生影响:一样平常来说,直径越大就越随意马虎产生浇口残留。
隧道浇口的情形也一样。在隧道浇口的情形下,乃至进入角度也会产生影响。角度偏小则随意马虎产生浇口残留;反之,过大则会产生浇口切割不良。这是由于在隧道浇口中,浇口前端孔的大小会随其角度的变革而变革(基本上是椭圆形)。
(2-3) 等级固有的问题
耐冲击性等级或合金材料比标准等级更随意马虎产生浇口残留。其缘故原由常日包括 1)掺入这些材料的不同树脂固化偏慢;2)由于在浇口附近承受很大的剪切力,因此所添加的不同树脂被拉伸成层状
(3) 浇口残留的对策
(3-1) 促进浇口固化
使浇口充分固化以减少浇口残留。详细方法如下:
•降落模具温度
•留足冷却韶光
(三十九)浇口切割不良
(1)何谓浇口切割不良
浇口切割不良的天生缘故原由
力方面的平衡不良
(2)等级固有的问题
(3)浇口切割不良的对策
变动强度平衡
(1) 何谓浇口切割不良
是指采取点浇口等成型时,连接成形品、主流道、分流道的浇口不易被割断的一种征象。若选用点浇口或潜伏浇口,在开模的同时,连接产品,主流道、分流道的浇口会自动断裂。但如果浇口的形状或大小不得当,则会产生浇口切割不良,并残留在模具内部
(2) 浇口切割不良的天生缘故原由
(2-1) 力方面的平衡不良
为了担保浇口处将产品部分与分流道部分割断,保持“浇口强度”、“分流道的保持力”以及“产品的保持力”等3个力的平衡是非常主要的。打开模具时,如果分流道部分留在固定侧,而产品部分留在可动侧,两者就会在浇口处被割断。如果浇口的强度太大,或产品部分与分流道的保持力偏弱,则会产生浇口切割不良
一样平常来说,分流道是通过锁定销来保持的;其保持力取决于锁定销的形状和大小以及开模时分流道部分的温度。如果锁定销的大小或斜度不敷,浇口就会在尚未被割断的时候脱落,因此与其增大浇口强度,倒不如增强分流道的保持力。相反,分流道的保持力过大则会使分流道无法分开模具。并且树脂的强度和刚性也会随着温度的变革而变革,因此也必须根据这一点进行调度。
产品部分是靠侧面斜度的摩擦力,或滑芯来保持的。在依赖斜度摩擦力保持的情形下,仍须达到浇口强度以上。此时也会受到温度的影响。
此外浇口强度当然会受浇口设计的影响。如果浇口尺寸偏大,强度就会增大,从而使浇口不易被割断。若是2块模板,且采取的是隧道浇口,则还会受到浇口角度及设置位置的影响。若是3块模板,且采取的是点浇口,则还会受到2次主流道的斜度、研磨等的影响。
(1)模具温度
受冷却后的树脂温度的影响。如果树脂温度发生变革,则强度和刚性也会随之变革。
(2)保压压力与保压韶光
受树脂添补量、产品、主流道和分流道的尺寸的影响。其尺寸对侧面的斜度摩擦保持情形有很大影响。尺寸过大时乃至会涌现无法脱模的情形。
(3)注射速率
受树脂添补量、产品、主流道和分流道的尺寸的影响。
(2-2) 等级固有的问题
就耐冲击性等级或合金材料等而言,添加了弹性体的树脂,其固化速率偏慢且材料的弹性模量降落,因此比其它材料更易涌现浇口切割不良。由此可见,在模具设计阶段就须要充分研究干系对策
(3) 浇口切割不良的对策
(3-1) 改变强度平衡
根据浇口切割不良的状况对成型条件进行如下调度
★分流道留在可动侧时
可认为是由于固定侧的分流道锁定销偏弱,或浇口部分的强度偏大。因此可采纳增大分流道锁定销的保持强度,或减弱浇口强度的对策。改动模具以改变两者的大小也是一个方法。如果要变动成形条件,则降落模具温度,促进分流道锁定销周围的固化和提高强度的方法也可能有效。如果是隧道浇口,也可以考虑改动浇口部分。
★分流道留在固定侧时
可认为是由于产品部分的侧面斜度偏弱,或浇口部分的强度偏大。对策之一,修正模具以强化斜度或减小浇口。另一种方法则是提高保压,增大分流道尺寸以提高保持力
★在3块式模具中产品和分流道留在中板上时
浇口太强的可能性很大,因此应将浇口尺寸轻微改小,或反过来强化分流道锁定销。就成形条件而言,减小保压也可能有效。
(四十)主流道粘模
(1)何谓主流道粘模
(2)主流道粘模的天生缘故原由
主流道固化不充分
•过度施加保压
•模具布局方面的问题
•等级固有的问题
(3)主流道粘模的对策
•使主流道充分冷却并固化后再开模
•降落保压
•改进模具
(1)何谓主流道粘模(外不雅观)
主流道残留是指成型品的主流道未能分开模具的一种征象。
如果永劫光施加保压甚至主流道尺寸增大,或模具的主流道部分有伤,则会产生阻力,从而使主流道在开模时不能脱落。
(2)主流道粘模的天生缘故原由
(2-1) 主流道固化不充分
主流道尚未完备固化时,由于此刻的紧缩量很小,主流道紧贴模具,强度也偏低,因此如果此时就要使主流道退出,则会非常随意马虎折断。这样一来,主流道就残留下来了。树脂温度、模具温度以及周期(冷却韶光)等对主流道固化都有影响。
(2-2) 过度施加保压
主流道部分离机筒喷嘴最近,因此便于施加保压。因此,施加高保压后,主流道的尺寸便会增大,而且脱模时的阻力也会相应地增大,从而随意马虎发生主流道粘模。
(2-3) 模具布局方面的问题
主流道部分的斜度偏小时,固定侧脱模的阻力会增大。虽然为了从固定侧拔出主流道而设置了主流道锁定,但如果很薄弱,锁定就会受损,从而使主流道从移动侧脱落。其余,如果利用的是分流道锁定,由于它过于稳定,主流道和分流道有时会粘附到固定侧。
(2-4) 等级固有的问题
与标准等级比较,耐冲击性等级或合金材料的紧缩更小,更随意马虎粘附到模具上,而且强度也更低。这样一来,主流道粘模就更随意马虎发生了。
(3)主流道粘模的对策
(3-1) 使主流道充分冷却并固化后再开模
降落模具温度并延长冷却韶光。特殊是对付强度小而固化慢的材料,降落模具温度将是一种有效方法。
(3-2) 降落保压
降落保压也是有效的。施加在产品模腔上的保压会在浇口封闭后变为0,因此,如果此后不施加保压,则主流道就不会承受无用的保压。但过度降落则随意马虎导致注射量不稳定,因此须要把稳。
(3-3) 改进模具
主流道斜度所必需的角度尚未有专门的规定。但如果可能涌现主流道粘模,则增大角度也是有效的。强化主流道锁定(加大尺寸并增强斜度)也是有效的。相反,由于有可能因顶出而变得难以脱落,因此须要在实际成型的同时进行调度。
分流道锁定过于稳定时,请将该部分的尺寸略微改小。
(四十一)表面剥离
(1)何谓表面剥离?
(2)表面剥离的天生缘故原由
•剪切力偏大
•混入不同材料
•大量气体混入表层
(3)表面剥离的对策
•降落剪切力
•抑制气体
(1) 何谓表面剥离(外不雅观)?
顾名思义,表面剥离是指成型品表层发生剥落的一种征象。
注射成形品的布局常日分为表层(称为皮层)和内层(称为芯层)。这是由于熔化了的树脂通过喷流进入模腔内,在表层固化的同时,内部还在流动。这两层界面因某种缘故原由而发生剥落的征象便是界面剥离。
(2) 表面剥离的天生缘故原由
(2-1) 剪切力偏大
剥离是因树脂流动时的剪切力过大而产生的。剪切力变大的条件如下。特殊是在厚度小且压力高的情形下随意马虎产生这种成型不良。
(1)机筒温度偏低(包括喷嘴)
(2)模具温度偏低
(3)浇口偏小(通过浇口时剪切力变大)
(4)产品厚度偏薄
(5)保压压力过高
(6)注射速度过快
此外还应把稳流动间隔、充填韶光是否过长。如果充填韶光长,则浇口附近的固化层和流动层的温差就会增大,从而随意马虎产生剥离。
(2-2) 混入不同材料
不同种类的树脂混入时也会产生剥离。塑估中具有相溶性(完备稠浊)的组合非常少,不同树脂可相溶的事例险些没有。在成型过程这些树脂被拉长变薄,在成形品内部呈层状并分散开来,从而随意马虎发生表层剥离。
与一样平常的等级比较,含油的滑动等级和合金材料更随意马虎产生表层剥离。
(2-3) 大量气体混入表层
含有大量气体时也会产生剥离。这是由于滞留在表层下面的气体会集聚成很薄的气体层。随意马虎产生气体的条件如下:
(1)机筒温度过高(树脂已经分解)
(2)干燥不敷(含有大量水分)
(3)螺杆转速过快(空气卷入)
(4)背压过低(空气卷入)
(5)保压压力过高
(6)注射速度过快
(7)利用了回收材料
(3) 表面剥离的对策
(3-1) 降落剪切力
有各种方法,但首先从容易改变的条件动手:
•提高机筒温度(包括喷嘴)
•提高模具温度
•减慢注射速率
•降落保压
此时,如果缘故原由在于气体,则提高机筒温度有时反而会使情形恶化。就机筒温度而言,一样平常应遵守相应的树脂的推举利用温度。
其次应检讨浇口和产品厚度。如果剥离发生在浇口附近,则缘故原由可能是浇口过小。如果产品厚度过薄,剪切力偏高,则应考虑利用流动性好的等级。其余,就浇口而言,侧浇口比点浇口或隧道浇口更可取,可能的话改变浇口设计也是一种方法。此外采取多点浇口也很有效果。
(3-2) 抑制气体
为使成型品不含无用气体,应检讨下列几点或履行相应的对策:
•检讨机筒温度是否在推举的温度范围内
•增强干燥温度
•降落过高的螺杆转速
•充分施加背压
•缩短成型周期
•降落回料的利用比率
(四十二) 喷射纹
1、何谓喷射纹?
2、喷射纹的天生缘故原由
・浇口尺寸偏小
・注射速率偏快
・粘度偏高/流动性偏低
・保压偏低
3、喷射纹的对策
・考试测验增大浇口尺寸
・考试测验变动浇口位置
・考试测验降落注射速率
・降落树脂粘度
・检讨保压
1、 何谓喷射纹?(外不雅观)
常日,溶融的树脂因此喷流的形式来流动的。不过,当从狭窄处流到宽阔处时,如果流速偏快,有时就会呈带状飞出,并且在不打仗模具的情形下流动。这被称为喷射纹。根据喷射纹在成品表面的表现办法,有的呈带状,有的则呈雾状,但它们的缘故原由都是一样的。
2、 喷射纹的天生缘故原由
(2-1) 浇口尺寸偏小
发生喷射纹的最大缘故原由是浇口尺寸。如果想象一下水枪,则不难明得喷射纹这一征象。孔(浇口)越小,飞出去的力量就越足,喷射纹也会因此而变得加倍严重。之以是说孔小是由于它意味着该处的压力增高,且速率加快。
(2-2) 注射速率偏快
在浇口直径相同的情形下,注射速率越快,喷射纹就越严重。
(2-3) 粘度偏高/流动性偏低
在浇口直径和注射速率相同的情形下,树脂的粘度越高(流动性越低),喷射纹就越严重。
影响粘度增高的条件如下:
(1)树脂温度偏低
(2)模具温度偏低
(3)材料粘度
(2-4) 保压偏低
保压在一定程度上会使喷射纹变得太不明显。相反,如果未充分施加保压,喷射纹就会很明显。
3、 喷射纹的对策
(3-1) 考试测验增大浇口尺寸
首先检讨能否变动浇口尺寸。虽然这取决于产品的形状和大小,但有余地的话,通过变动浇口尺寸是可以肃清喷射纹的。最好采取短而宽的浇口流道(gate land);呈扇状打开并带有角度的设计样式也很有效。
(3-2) 考试测验变动浇口位置
接着检讨能否变动浇口位置。喷射纹基本上是由于树脂飞出去的力量很大而产生的。而且飞出去的目标空间越开阔就越严重。但如果从浇口飞出去的树脂很快碰钉子的话,喷射纹即可肃清。
纵然在无法变动浇口位置的情形下,如果能够在产品模腔内的浇口正面其余设置针或壁之类的东西,则有望得到同样的效果。
(3-3) 考试测验降落注射温度
考试测验降落注射速率设定。对策是采取多段注射并且只减慢通过浇口时的速率(而非整体降落)。
◆各种材料的推举注射条件
树脂 注射压力 注射速率 V-P切换位置
Duracon max8~19mm/sec 制品添补量的9成旁边
Duranex 〃 16~33mm/sec 〃
Fortron 〃 25~42mm/sec 〃
Vectra 〃 30~50mm/sec 〃
(3-4) 降落树脂粘度
降落树脂粘度的方法:
(1)提高树脂温度
(2)提高模具温度
(3)将等级改为高流动型
(3-5) 检讨保压
◆各种材料推举的保压条件
树脂 保压力 保压韶光
Duracon 59~98MPa 浇口密封+1~2sec
Duranex 59~98MPa 〃
Fortron 39~69MPa 〃
Vectra 29~49MPa 〃
(四十三)流涎
1、 何谓流涎
1、 流涎的天生缘故原由
•树脂粘度偏低
•机筒内压偏高
3、 流涎的对策
•提高树脂粘度
•降落内压
•变动喷嘴形状
1、何谓流涎(外不雅观)
指树脂从成型机喷嘴漏出的一种征象。
一样平常的注射成型机的喷嘴前真个树脂并没有完备固化,当机筒内压偏高,或树脂粘度偏低时,已熔化的树脂就会漏出。
树脂粘度偏低或成型机机筒的内压偏高时就会涌现流涎。
2、 流涎的天生缘故原由
(2-1) 树脂粘度偏低
大部分注射成型机都采取开式喷嘴,并通过条件调节来防止外流。但是,如果分子量因分解而降落,或把机筒的设定温度设得很高,树脂就会因粘度降落而流出。
(2-2) 机筒内压偏高
对机筒内的树脂施加一定压力的缘故原由有2点:一个是气体的膨胀,另一个是计量时的背压。
气体膨胀的缘故原由是树脂的分解气体和粒估中的水分。它们气化并膨胀后,无处可去的压力就会流向喷嘴的前端,从而形成流涎。
另一方面,就背压而言,由于计量时须要用它来防止空气卷入,因此必须施加一定程度的背压。但如果施加过度,树脂就会被压缩成紧缩状态,从而导致内压升高和流涎。
其余,空气也会因加热而膨胀起来,因此如果计量时卷入了大量空气,流涎就会加倍严重。
3、流涎的对策
(3-1) 提高树脂粘度
把机筒温度、特殊是喷嘴温度设得略低一些。设得过低则会影响流动性并产生冷料(混入熔化不敷的树脂)等,进而造成外不雅观不良,因此建议利用推举温度范围内的最低限。此外,把材料等级改为粘度更高的材料也是一种有效方法。
(3-2) 降落内压
首先降落螺杆转速和背压。但如果背压为0,则随意马虎卷入气体,并有可能造成其它成型不良,以是最低也要施加约0.2Mpa的背压。螺杆转速应设在100rpm旁边。
从防止气体混入的意义上来说,可采纳下列有效方法:(1)加强干燥,(2)不要把机筒温度升得太高。此外,增大抽塑量也有效。抽塑可使螺杆退却撤退,从而在整体上减少树脂。这样便可在前部形成间隙,从而赢得流涎发生前的韶光。
(3-3) 变动喷嘴形状
出于规格的简便性以及本钱方面的考虑,一样平常的成型机都采取开式喷嘴,对付流涎确实很严重的材料,利用闭式喷嘴也是一种办理方法。此外,喷嘴的孔径越小,则越难以形成流涎。许多成型机生产商都备有不同孔径和形状的喷嘴。价位大多在10万日元以下,值得购买。不过,由于材料的流动性偏低,因此条件是成型条件要有一定程度的余地
(四十四) 注射量不稳定
1、何谓注射量不稳定
2、注射量不稳定的天生缘故原由
•压力不敷
•模具温控不稳定
•计量不稳定
•排气不良
3、注射量不稳定的对策
•充分施加保压
•重新检讨模具温控
•使计量保持稳定
•改进排气状况
(1)何谓注射量不稳定
是指每模所得成型品之间存在偏差。
成型品在尺寸、外不雅观、重量等方面的不稳定是由成型条件的差异所引起的。
(1)注射压力
(2)模具温度
(3)计量
(4)排气
上述成型条件的不稳定是其紧张缘故原由。
(2)注射量不稳定的天生缘故原由
(2-1) 压力不敷
一样平常的注射成型工序为注射→保压→冷却(计量)。注射~保压阶段该当是通过加压来压入已融化树脂的过程。该压力偏低时被压入的树脂量就随意马虎变得不稳定。产生这种压力不敷的缘故原由多种多样,详细如下:
•树脂温度偏低
•模具温度偏低
•注射速率偏慢
•保压偏低
•保压韶光偏短
•VP切换位置过早
•主流道、分流道、浇口等的信道部分偏细,从而导致压力通报不畅
•树脂流动性差,因此压力丢失大。
•厚度中有特殊厚的部分。
(2-2) 模具温控不稳定
模具温控不稳定时特殊随意马虎伴生尺寸的偏幸或偏差等。根据模具的详细情形,有时也难以对塑孔栓等进行局部温度调度,从而使偏差加剧。
(2-3) 计量不稳定
若计量不稳定,注射的树脂量也就不稳定。这样一来,各次注射之间涌现偏差的可能性也就增大了。详情请参阅计量不良部分。
(2-4) 排气不良
排气口偏弱、排气不畅时,添补量有时会变得不稳定。
(3)注射量不稳定的对策
(3-1) 充分施加保压
由于某种(即便是局部性的)缘故原由,实际的保压力存在不稳定的可能性。因此应采纳下列对策。由于均匀尺寸会因此而偏大,因此就工序管理而言,有必要设定不同的标准。
★成型条件
•提高树脂温度
•提高保压力
•提高模具温度
•延长保压韶光
•加快注射速率
•延迟VP切换位置
★模具
•扩大主流道、分流道、浇口等
•尽可能使壁厚均一化。厚度标准为2-4
★材料
•改用流动性好的材料
(3-2) 检讨模温机
水温掌握时,请检讨存在问题的部位附近的温控信道是否畅通。特殊是塑孔栓等处的温度很随意马虎升高,因此应尽可能对其进行温度掌握。如果是电加热器,则请检讨加热器的位置。
(3-3) 使计量保持稳定
请参阅此处的计量不良对策并予以履行。
(3-4) 改进排气状况
偶尔也有排气口排气不畅、尺寸不稳定的情形。此时须要降落注射速率,或强化排气口以使排气通畅。
(四十五)紧缩(Sink marks)
何谓紧缩
塑件表面材料堆积区域有凹痕。紧缩水紧张发生在塑件壁厚厚的地方或者是壁厚改变的地方。
物理缘故原由
当制品冷却时,紧缩(体积减小,紧缩)发生,此时外层紧模壁的地方先冻结,在制品中央形成内应力。如果应力太高,就会导致外层的塑料发生塑性变形,换句话说,外层会朝里凹陷下去。如果在紧缩发生和外壁变形还未稳定(由于还没有冷却)时,保压没有补充熔料到模件内,在模壁和已凝固的制品外层之间就会形成沉降。
这些沉降常日会被算作为紧缩。如果制品有厚截面,在脱模后也有可能产生这样的缩水。这是由于内部仍有热量,它会穿过外层并对外层产生加热浸染。制品内产生的拉伸应力会使热的外层向里沉降,在此过程中形成紧缩。
与加工参数有关的缘故原由与改良方法见下表:
1、保压太低增加保压
2、保压韶光太短延长保压韶光
3、模壁温度太高低降模壁温度
4、熔料温度太高低降熔料温度,降落料筒温度
与设计有关的缘故原由与改良方法见下表:
1、料头横截面太小增加料头横截面
2、料头太长缩短料头
3、喷嘴孔太小增加喷嘴孔径
4、料头开在薄壁处将料头定位在厚壁处
5、材料堆积过量避免材料堆积
6、壁/筋的截面不合理提,供较合理的壁/筋的截面比例