自动生产线是在流水线的根本上逐渐发展起来的,是通过工件传送系统和掌握系统,将一组数控机床和赞助设备按照工艺顺序联结起来,自动完成产品全部或部分制造过程的生产系统。
- 文章信息 -
本文引自:《智能制造装备根本》。作者:吴玉厚、陈关龙、张珂、赵德宏、巩亚东、刘春时。由「智造苑」原创首发, 数字化企业经授权发布。
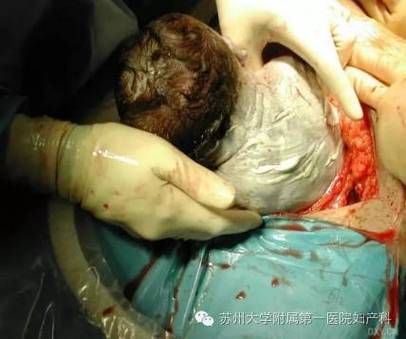
在全体自动化生产线中,其详细组成所包括的内容共有13个部分,紧张为各个功能站点、不同功能模块、传感器、电磁阀及进出口接口等干系内容。个中,功能站点紧张包括工料站、加工站、装置站与搬运站、成品分拣站;在各种不同模块中,共包括5种类型,分别为变频器模块、电源模块、PLC模块与按钮模块、电机驱动模块。在对这些部分进行集成的根本上,自动化生产线不但能够实现高下料及加工,同时还能够完成装置、分拣以及运送等干系内容。
智能车床及车削中央作为单机产品,能够知足一样平常小型大略零件的生产制造,然而随着工业生产模式向自动化和柔性化转型升级,传统的流水线作业已经无法知足现有高精度、高效率、高柔性的生产哀求,因此,基于智能机器人和智能车床、智能车削中央发展起来的智能车削生产线,将会成为生产自动化的紧张发展方向。智能车削生产线涉及生产线总控、质量检测、搬运机器人、加工机床、物流运输线、生产管理和成品仓储等设备,每一台设备都是智能车削生产线中的主要组成部分。由多条智能生产线,通过进一步的系统集成,将能够形成数字化车间和数字化工厂,实现全体工厂的自动化和智能化。
智能生产线总体布局
图1所示是一条范例的智能车削生产线,紧张完成零件从毛坯到成品的混线自动加工生产。车削生产线由产线总控系统、在线检测单元、工业机器人单元、加工机床单元、毛坯仓储单元、成品仓储单元和RGV小车物流单元组成,加工设备采取陕西宝鸡机床集团有限公司生产的CK系列智能机床,该机床装载了宝鸡B80智能数控系统。
图1 智能车削生产线[1]
1)总控系统和检测单元
图2所示为陕西宝鸡机床集团有限公司设计的范例总控系统,由室内终端和现场终端两部分组成。室内终端配备多台显示器及数据库,数据库卖力吸收全体生产车间传输过来的制造生产大数据,显示器用于用户车间现场各项状态的显示,包括设备运行状态、零件加工状态、物流情形、职员状况以及用户车间现场温度、湿度等环境信息,高层管理职员在室内终端可以非常方便、直不雅观清晰地查看现场的各项状况。
在用户生产车间中,配备现场终端,用于掌握全体生产线的现场运行,完成设备根本数据的采集、剖析、本地和远程管理、动态信息可视化等操作。现场终端配备显示器,通过显示器可以清晰方便地查看用户车间的各项状态,包括设备监控、生产统计、故障统计、设备分布、报警剖析、工艺知识库等。现场终端可以添加生产管理看板、实现加工程序的上传***、职员刷卡身份识别以及生产任务的进度统计与剖析等功能,可以通过有线、Wi-Fi、2G/3G/4G/5G等多种接入办法进行现场数据的采集与传输,搜集到的干系制造大数据可通过互联网传输到用户室内终真个SQLServer数据库中,通过终端打算机与室内终端进行数据交互。
图2 总控系统[2]
图3所示是范例的在线检测单元,由工业机器人、末端实行器和多源传感器等组成。物流系统将成品运输到指定位置之后,工业机器人将全体检测单元移动到指定工位上,通过视觉相机对待检测零件进行拍照识别和定位,工业机器人再次调度自身位置,使全体检测单元对准待检测部位。
图3 在线检测单元
个中,识别与定位完成之后,由末端实行器卖力待检测零件的抓取,通过工业机器人将零件转移到检测台上的指定位置,由检测台上预先配备的多源传感器对待检测零件的孔径、窝深、曲率、粗糙度、齐平度等精度指标进行在线检测,也可以通过智能算法对零件进行自动丈量和自动分类,将不同类型的零部件转移到不同的物流线上,完成零件的自动分类操作。检测单元通过互联网可以将检测结果返回给总控系统,操作职员通过室内总控系统或者现场总控系统的终端电脑和显示器可以直接不雅观看到零件的检测结果,符合检测哀求的,直接进行下一工位操作,不符合哀求的,在显示器上显示不合格提醒,由操作人根据零件的不合格程度进行剖断与决策。在检测完成之后,末端实行器抓取已检测零件,工业机器人将已检测零件转移到物流系统上,由物流系统运送到下一工位进行处理。
2)工业机器人和车削机床单元
图4所示是陕西宝鸡机床集团有限公司设计制造的加工模块,由工业机器人和车削机床两部分组成。个中,工业机器人卖力待加工零件的移动和抓取,车削机床为智能机床,能够担保高精度和加工效率。
图4 加工模块
物流配送系统将毛坯零件或者半成品零件运输到指定工位之后,由工业机器人抓取毛坯零件或者半成品零件,将其放入智能车削机床中,赞助机床完成待加工零件的装夹事情。对付双工位车削机床,在个中一台智能车床完成车削事情之后,由工业机器人将半成品零件转移到其余—台智能车床中完成下一工位的加工。待所有的加工事情完成之后,由工业机器人将成品零件抓取转移到物流系统中,由物流系统将零件转移到下一工位。
车削机床配备了智能康健保障功能、热温度补偿功能、智能断刀检测功能、智能工艺参数优化功能、专家诊断功能、主轴动平衡剖析和智能康健管理功能、主轴振动主动避让功能和智能云管家功能[3]。智能机床的紧张浸染是与工业机器人合营完身分歧阶段的加工生产任务,同时担保零件加工生产的效率和精度。用户可以根据生产车间须要,将智能机床改换为不同档次的机床,如高速车削机床、精密车削机床和加工中央等,也可以根据自身须要增加或减少相应的智能化功能,以组成最适宜企业生产需求的车削生产线。
3)物流与成品仓储单元
图5所示是陕西宝鸡机床集团有限公司设计和生产的范例物流单元,由工业机器人、末端实行器、RGV小车、零件托运工装和行走轨道组成,紧张实现机床加工零件的转移运输事情。在用户车间中,根据生产任务的需求,智能生产线可以选择配备单条或者多条物流生产线。机床较少或者加工任务较为大略的智能车削生产线,可以采取单物流线模式,完成上料、转移和下料等操作;机床任务较多或者加工任务较为繁芜的情形,为了避免物流系统的任务繁杂和冲突,
可以配备两条或者多条物流线,一条用于毛坯零件或者半成品零件的上料,—条用于中间过程的转运,—条用于成品零件的下料。对付加工场景较为大略的智能车削生产线,工业机器人可以固定不动,即可完成零件的装夹和取放;对付较为繁芜的智能车削生产线,可以再单独配备移动机器人,在行走轨道上进行零件的分配、抓取和释放工作。各工位之间的零件转移由RGV小车完成,通过自动编程,RGV小车能够在指定时间内准确无误地到达预定的位置,以担保工业机器人能够顺利识别并抓取零件。RGV小车上配备零件托运工装,用户车间可以根据加工零件的大小及尺寸,配备不同的工装,待工装各位置已装知足够的毛坯零件或者成品零件后,RGV小车运行,完成相应的上料、转运和下料事情。
图5 物流单元图6成品仓储单元
图6所示是陕西宝鸡机床集团有限公司设计和生产的范例成品仓储单元,由仓储柜、工业机器人、末端实行器、行走轨道组成。零件在完成加工之后,由RGV小车将成品零件转运到下料区,工业机器人移动到下料区,末端实行器根据成品零件编号,将成品零件进行抓取,再由工业机器人将成品零件转移到仓储柜的指定位置。末端实行器须要各用户单位根据加工零件的形状、尺寸进行分外设计,以知足不同零件的抓取事情。仓储柜由大小相同的独立小柜构成,各小柜之间可以快速地拼接和拆分。对付固定式工业机器人,用户车间应该根据工业机器人的最大事情高度和最大事情范围,自行调度设计仓储柜长度和高度。
配备行走轨道的工业机器人,成品仓储柜可以设计得相对长一些。机器人通过行走轨道,能够增加事情覆盖范围,行走轨道可以根据需求,设置为直线形或者环形。对付有多个仓储柜的用户车间,或者有不同零件分类的成品仓储柜,用户单位也可以调度行走轨道的长度和形状,如环形轨道就能使一台机器人对应多个成品仓储柜,实现—台机器人多做事,提高机器人利用率。成品物流仓储柜数量较多的时候,应该增加行走轨道的长度,或者配备两个及以上的工业机器人以担保物流的效率。须要把稳的是,行走轨道长度设计要考虑机器人的行走韶光,不能设计得过长,如果机器人行走韶光过长,则可能导致物流配送效率低,造成成品零件不才料区涌现堆积,产生零件碰撞等意外,这样反倒增加了生产风险,同时也降落了事情效率。
机床掌握器的掌握层级
人工智能与打算机技能的结合,极大地推动了数控系统的智能化程度,紧张表示在数控系统中的各个方面:
(1)运用前馈掌握、在线辨识、掌握参数的自整定等技能提高驱念头能的智能化;
(2)利用自适应掌握技能实现加工效率和加工质量的智能化;
(3)运用专家系统等智能技能实现故障诊断、智能监控等加工过程掌握方面的智能化。
制造过程中,机床掌握器的掌握层级可以划分为图7所示的3个层级,包括电机掌握层级、过程掌握层级和监督掌握层级。个中,电机掌握层级可以通过光栅、脉冲编码器等机床检测设备实现机床的位置和速率监控;过程掌握层级紧张包括对加工过程中的切削力、切削热、刀具磨损等进行监控,并对加工过程参数做出调度;监督掌握层级是将加工产品的尺寸精度、表面粗糙度等参数作为掌握目标,以提高产品的加工质量。
图7 机床掌握器的掌握层级
1)智能化加工掌握国外发展趋势
◉ 智能掌握策略研究:在神经网络掌握加工领域,专家提出了一种粒子群驱动的鱼群搜索算法,用来优化数控机床加工参数。神经网络须要进行过程迭代、收敛受网络繁芜度的影响要花费一定韶光的问题,为理解决这一问题,提出了基于神经网络和遗传算法的稠浊方法以减少神经网络的打算繁芜度和韶光花费,并对平面加工的特色识别进行仿照实验,证明其可行性。有人提出了一种基于遗传算法,适用于求解眇小的切削力预测模型,该模型可以实现对切削力的预测和对切削参数的优化。
◉ 加工过程的监控运用:监控监测加工过程中的不正常征象,进而采纳停滞加工过程、调度加工过程参数(如主轴转速)以避免机床毁坏。加工过程的不正常征象可能是渐进产生的,如刀具磨损;也可能溘然产生,如刀具破损;或者可以预防,如振动或颤振。
2)智能加工掌握海内发展趋势
在智能化掌握下,自动化系统能够主动对故障进行检修,由于自动化系统在运用过程当中能够很好地将所有的机器通过打算机措辞联系在一起,并产生一个具有联动性的处理系统。根据采取的传感器、掌握方法和掌握目标的不同,对加工过程监控的研究紧张集中在以下几个方面:
①通过对刀具磨损的研究,实现加工状态监控;
②通过对测力仪或丈量电机电流等间接办法得到的切削力的研究,对加工过程状态进行改进;
③CAM领域的离线参数优化研究;
④智能加工掌握算法仿真研究等。
数控机床全生命周期管理做事平台
智能制造是面向产品全生命周期,实现泛在感知条件下的信息化制造。数据和信息是智能制造中流动着的“血液”,数字化将数据转变成信息,通过网络化和智能化决策创造出有用的代价,因此,智能产品制造都是由数据驱动的。产品全生命周期建档分为4个阶段。
①部件生产阶段:采购环节数据、生产环节数据、测试入库记录;
②配套产品入库阶段:配套产品入库检测记录、配套产品采购订单信息;
③机床整机调试阶段:机床制造过程数据、机床出厂测试调机数据、机床出厂记录;
④机床交机阶段:用户开机、调机数据记录、自主维修、—键报修、用户维修记录、用户利用过程数据。
数控机床全生命周期管理做事平台运用物联网、云做事、大数据等关键技能,采集数控机床从设计、加工到机床整机调试,用户交机利用等全生命周期数据,建立机床档案数据库,进行全生命周期信息追溯,为用户供应远程设备监控、生产统计管理、设备运行掩护等做事。图8所示为陕西宝鸡机床集团有限公司的宝鸡云(BOCHICLOUD)技能架构。宝鸡云的核心亮点是其运维做事功能:
(1)故障案例知识库:为用户供应故障办理方案;
(2)故障报修:设备故障在线报修、报修订单及时叮嘱消磨、工程师快速跟进等;
(3)定期保养:跟踪设备全生命周期性能变革,供应定制化保养操持;
(4)预测性掩护:预测设备潜在的故障风险并及时备件。
图8 BOCHICLUD技能架构[4]
数字化生产线系统集成
随着集成掌握系统技能的快速发展,自动化生产线向着更高的自动化和集成化方向发展。生产线集成掌握是通过某种网络将个中须要连接的智能设备进行组网,使之成为一个整体,使其内部信息实现集成及交互进而达到掌握目的。生产线集成掌握的种类有设备集成和信息集成两种。设备集成是通过网络将各种具有独立掌握功能的设备组合成一个有机的整体,这个整体是一个既独立又关联而且还可以根据生产需求的不同而进行相应组态的集成的掌握系统。信息集成是利用功能模块化的设计思想实现资源的动态调配、设备监控、数据采集处理、质量掌握等功能,构成包括独立掌握等处理功能在内的基本功能模块,各个功能模块实现规范互联,布局功能单元时采取特定的掌握模式和调度策略,达到预期的目标,进而实现集成掌握。
传统的自动化企业专注于设备级的自动化实现,但对上层SCADAMES/ERP等系统不熟习,致使忽略生产线信息的数字化获取及生产信息的横向、纵向流动。MES/ERP等软件系统企业专注于上层系统级的数据剖析与调配掌握,对付底层型号互异的实行设备和掌握器等硬件设备以及掌握办法难以涉及,影响信息纵向流动。通过数字化丈量实现制造信息(关键参数)的数字化获取及流转,可打通上层系统与底层生产线之间的阻隔,开释已有的优质生产力,加快我国制造业发展进程。通过集成工装设计、制造、管理技能,构建工装数字化生产线,实现工装研发过程各环节数据流的畅通,才能充分发挥数字化技能在工装研发过程中的浸染,从而提高工装制造精度和效率,缩短研制周期,降落研制本钱。
生产线集成掌握是将通信、打算机及自动化技能组合在一起的有机整体。为了使生产线中各设备和分系统能够折衷事情,系统采取PLC及其分布式远程I/0模块实现生产单元的“集中管理、分散掌握”;同时PLC吸收来自上位MES系统的管理,包括操作职员信息核对、产品掌握、物料管理等信息。生产线掌握系统构造如图9所示,通信内容包括操作职员身份识别、生产线线体状态、机器手信息、机器人信息、工件加工信息、机床事情状态及各种故障信息等。
图9 生产线掌握系统构造示意图
掌握系统硬件组态如图10所示,采取PROFINET网络与底层的现场IO设备通信, IO设备包括IM151-3PN现场模块、ET200ecoPN输入输出模块、RF180C通信模块等具有以太网功能的模块。为了与车间其他单元PLC系统数据共享,掌握系统还配备了工业级PN/PN耦合器,通过该网桥,可以实现自动生产线与车间其他PLC系统之间的信息交互。同时,为了担保生产的可靠性,在各单元的掌握器间采取光纤环网连接,一旦MES系统涌现故障,掌握系统可以分开MES系统正常运行。
图10 掌握系统硬件组态
参考文献[1]樊军锋.智能工厂数字化交付初探[J]. 石油化工自动化,2017,53(3):15-17.
[2]余勤锋.石化工程企业设计集成系统的构建[J]. 当代化工,2015,35(8):6-10.
[3]李其锐.基于设计集成系统海洋平台项目复用及模板化设计的运用[J]. 中国勘察设计,2013(9):97-100.
[4]陈文静.智能化技能在自动掌握工程领域的运用研究[J]. 智库时期,2019(4):25-255.