芯轴多传感器在位丈量。国防科技大学供图
超精密机床根本部件加工与运用技能的打破,能为制造业的生存和发展供应强大技能支撑。然而此前我国超精密机床及关键根本部件紧张依赖入口。
国内外轴类零件外圆圆度加工,基本都是靠超精密的外圆磨床实现。以磨削直径100毫米、长300毫米的轴芯为例,我国外圆磨床大概能够磨到1至2微米的水平,而国外可达到0.3至0.5微米的水平。
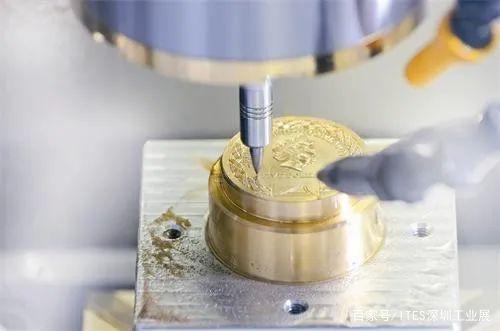
为破解机床和关键部件技能难题,国防科技大学教授戴一帆团队历时5年,提出轴类零件外圆圆度确定性修形加工工艺技能,使轴芯加工圆度精度提升到0.1微米,并成功研制出超精密空气静压主轴。近日,经中国计量科学研究院测试,该静压主轴干系参数达到国际前辈水平,这将有效提升我国超精密加工精度。干系研究成果先后揭橥于《材料》和《微型机器》。
像铁锹整地那样研磨超精密零件
我国超精密机床及关键根本部件此前之以是紧张依赖入口,最大的技能难题在于短缺加工核心零件的“事情母机”,即制造机器和机器的机器,又称工具机,包括车床、磨床、刨床、钻床等,是制器之器、工业自强之基。
一样平常的机器加工是将机床精度“复印”到零件的过程,也便是说,没有精度高的机床就加工不出精度高的零件。没有精度高的零件,就组装不出精度高的部件和机床。没有制造高精度零件的事情母机,就限定了全体超精密机床行业的发展。
戴一帆团队长期从事当代光学制造技能研发,他们创造光学零件的终极制造精度远超所利用的加工设备精度,而光学制造的基本事理是逐步将偏差高点去除的精度进化加工。团队考试测验将这种“精度进化”事理的加工方法用于机器零件高精度加工,终极通过加工事理的创新提出轴类零件外圆圆度确定性修形工艺技能,打破高精度“事情母机”的限定。
确定性修形工艺是如何事情的?“这就像利用铁锹平整一块地,即在看上去突出不平的地方铲去适量的土,如此反复,直到得到非常平整的地。”戴一帆说,这个过程依赖的是成套数字扮装备,包括获取圆柱描述的高精度圆度仪、实现材料去除量数字化精确可控的控时磨削机床、得到磨削工具在特定空间位置勾留韶光的专用打算机程序等。
机器取代有履历的工人师傅
借助新工艺,戴一帆团队打破了基于精度进化事理的控时磨削加工技能,形成了圆柱类零件在位加工检测一体工艺方法,成功研制出超精密空气静压主轴。
中国计量科学研究院测试结果显示,该空气静压主轴径向跳动小于15纳米、端面跳动小于15纳米。这个跳幅相称于头发丝直径的六千分之一。如果是地球这么大一根主轴的话,回转运动造成的振幅不会超过1米。
测试结果显示,空气静压主轴径向静刚度大于200牛每微米、轴向静刚度大于200牛每微米。普通地说,便是主轴可以在20公斤的重力载荷下纹丝不动,变形量不会超过1微米,即头发丝直径的百分之一。比拟代表美国超精密领域最高水平的Precitech公司的产品手册,上述技能指标与其相称乃至更高。
当前,国内外可将轴类零件外圆圆度加工研磨到零点几微米的水平,如果再想提升只能靠手工研磨修整。“我们的新技能可以摆脱对极其有履历的工人师傅的依赖,能很随意马虎地按照当代工业化的模式组织生产,促进超精密根本部件的大批量、高效率生产和运用。”戴一帆表示,超精密机床根本部件加工与运用技能的打破,将为制造业的生存和发展供应强大技能支撑,完善高端机床家当链配套,大幅增强高性能功能部件竞争力,促进高端精密与超精密机床实现国产化。
戴一帆补充说,这些打破还将有效办理探测制导关键零部件超精密加工面临的超精密装备和核心工艺难题,进一步助力高端核心零件超精密加工批量化生产,实现科研成果的快速转化。
干系论文信息:
https://doi.org/10.3390/ma13112458
https://doi.org/10.3390/mi14061240
https://doi.org/10.3390/mi14030653